Страница для печатиМ. X. Зиатдинов1, И. М. Шатохин2
1 - Томский государственный университет (г. Томск, Россия)
2 - ООО "НТПФ "Эталон" (г. Магнитогорск. Россия)
Исследования процесса самораспространяющегося высокотемпературного синтеза (СВС) в системе феррованадий — азот позволили создать новую промышленную технологию производства азотированных ферросплавов. СВС-технология характеризуется отсутствием потребления электроэнергии, экологической безопасностью и хорошими эксплуатационными характеристиками продукта.
Выпуск высокопрочных низколегированных сталей (HSLA-steels) постоянно увеличивается благодаря большой экономической эффективности их использования. Строительство и автомобильная индустрия, мосто- и судостроение, железнодорожный и трубопроводный транспорт — вот неполный перечень отраслей экономики, в которых эти стали практически незаменимы. Высокие эксплуатационные характеристики их достигаются микролегированием такими карбидо- и нитридообразуюшими металлами, как Аl, Ti, V, Nb и др. При охлаждении и в результате применения специальных режимов прокатки и термообработки в металлическом слитке выделяются мелкодисперсные карбиды, нитриды и/или карбонитриды указанных металлов. Размеры выделений обычно составляют от нескольких до десятков нанометров. Такие нанокомпонентные стали прочны, пластичны, хорошо свариваются и сохраняют свои эксплуатационные характеристики при экстремально низких температурах. Среди большого разнообразия марок высокопрочных низколегированных сталей особой экономичностью выделяются стали, микролегированные ванадием и азотом при помощи азотированного феррованадия. Нитриды и карбонитриды ванадия, образующиеся в стали при охлаждении и термомеханической обработке в виде мельчайших наноразмерных частиц, способствуют сильному измельчению зерна. Совместное воздействие механизмов дисперсионного упрочнения и измельчения зерна приводит к качественному улучшению всего комплекса механических характеристик стали.
В настоящее время в сталеплавильном производстве микролегирование азотом проводят или азотсодержащим газом, или специально полученными лигатурами. Причем на практике часто одновременно используют оба легирующих способа. Часть азота поглощается расплавом непосредственно из газовой фазы, а окончательную корректировку состава осуществляют азотсодержащим сплавом. Такой легирующий сплав с азотом может применяться как в традиционном кусковом виде, так и в качестве наполнителя порошковой проволоки. Со времени начала разработки и производства HSLA-сталей с нитридванадиевым упрочнением в 1960 — 1970 гг. было предложено множество различных сплавов для их совместного введения в сталь. Эти сплавы получали либо твердофазным азотированием порошков, либо азотированием расплавов. Однако в настоящее время практически используют лишь два материала: азотированный феррованадий и карбонитрид ванадия, которые производятся по твердофазной технологии. Карбонитрид ванадия был разработан более 30 лет назад и известен в настоящее время как сплав NITROVAN. Среди привлекательных сторон этой лигатуры можно отметить высокое содержание азота (до 16 %) и то, что получают его непосредственно из оксида ванадия углеродотермическим восстановлением в вакуумных печах. Сложности применения карбонитрида ванадия на практике связаны с его высокой температурой плавления (> 2400 °С) и низкой плотностью брикетов (~3 г/см3). При выплавке стали это приводит к тому, что снижается степень усвоения не только азота, но и ванадия. Кроме того, азот нестабильно поглощается расплавом от плавки к плавке. Аналогичная картина наблюдается и при использовании в качестве азотированного феррованадия, полученного в вакуумных печах. Для производства нитрида феррованадия также используют печную технологию, сырьем в этом случае являются порошки стандартного феррованадия.
Растворимость азота в жидком феррованадии сравнительно высока. Сплав, содержащий 41,5 — 50,6 % V, при 1900 °С и атмосферном давлении растворяет 3,8 — 5,3 % N. Количество растворенного азота снижается при повышении температуры и уменьшении давления азота в феррованадиевом расплаве, азотирование жидких сплавов с целью получения литых лигатур не получило промышленного применения из-за высокой вязкости жидкого азотированного феррованадия а также трудности достижения в них больших концентраций азота в агрегатах большого объема.
По-видимому, не имеет практических перспектив и технология получения азотосодержащих феррованадиевых лигатур с использованием плазменной плавки вследствие ее исключительной дороговизны и низкой концентрации азота в конечном продукте.
Таким образом, единственной реальной альтернативой печной технологии производства азотсодержащих легирующих сплавов является СВС-метод. Самораспространяющийся высокотемпературный синтез, или синтез горением, изначально был предназначен для получения порошков бескислородных тугоплавких неорганических соединений. Он основан на высокой экзотермичности реакций образования таких соединений, как карбиды, нитриды, бориды, силициды. Позже СВС-метод был приспособлен для синтеза композиционных легирующих сплавов и других материалов, применяемых в металлургии. В основу такого варианта СВС-процесса, получившего название "металлургического СВС-процесса", были положены обменные бескислородные экзотермические реакции с использованием различных ферросплавов в качестве основных сырьевых материалов.
Настоящая работа посвящена разработке промышленной СВС-технологии получения азотированного феррованадия, предназначенного для выплавки высокопрочных низколегированных сталей. Предварительные лабораторные исследования осуществлялись с использованием в качестве сырья промышленных феррованадиевых сплавов различного состава по ГОСТ 27130-80 (таблица 1), а также металлического ванадия, выплавленного металлотермическим способом, по ТУ 48-20-72 чистотой 97,8 % V. Кроме того, при изучении возможности производства различных комплексных лигатур с азотированным феррованадием использовались порошки стандартных марок ферросилиция (ФС75, ГОСТ 1415-78), марганца (Мн95, ГОСТ 6008-90), феррониобия (ФН660, ГОСТ 167730-85).
Таблица 1. Состав исходных ферросплавов, %
Марка феррованадия |
V (Nb) |
Mn |
C |
Si |
Al |
S |
P |
FeV80 |
78,8 |
0,3 |
0,10 |
0,71 |
1,61 |
0,02 |
0,05 |
FeV60 |
59,2 |
0,2 |
0,06 |
0,80 |
1,25 |
0,02 |
0,05 |
FeV50 |
52,4 |
2,6 |
0,18 |
1,11 |
0,02 |
0,02 |
0,07 |
FeV40 |
41,6 |
3,4 |
0,25 |
1,37 |
0,02 |
0,02 |
0,08 |
FeNb60 |
(60,6) |
- |
0,08 |
1,01 |
2,1 |
0,01 |
0,07 |
FeSi75 |
- |
- |
0,07 |
76,7 |
1,1 |
0,005 |
0,02 |
Mn95 |
- |
96,3 |
0,09 |
0,7 |
- |
0,02 |
0,05 |
В ходе исследований установили, что в системе ванадий-азот образуются два устойчивых нитрида δ-VN (с областью гомогенности в пределах VN0.68-VN0.93) и β-V2N (VN0.37-VN0,43), а также α-твердый раствор азота в ванадии. Кроме того, при определенных режимах охлаждения и термообработки в структуре азотированного ванадия могут выделяться ряд нестабильных фаз: V16N, V13N, V9N, и др. Физико-химические и термодинамические свойства стабильных нитридов ванадия сильно изменяются в пределах области гомогенности. Например, температура плавления мононитрида ванадия снижается с максимального значения 2340 ˚С для VN0,98 до ~ 2260 ˚С для VN0,7. Взаимодействие ванадия с азотом сопровождается выделением большого количества тепла. Тепловой эффект реакций образования стехиометрического нитрида ванадия VN составляет 217,2 ± 5 кДж/моль, а V2N соответственно 270,6 ± 5,1 кДж/моль. Тепло выделяется также и при растворении азота в ванадии. Столь высокая экзотермичность реакций нитридообразования и позволяет осуществлять процесс насыщения азотом ванадия в режиме самоподдерживающегося горения в широком диапазоне изменения параметров процесса.
Большое тепловыделение при синтезе нитридов ванадия является энергетической основой при получении промышленного СВС-азотированного феррованадия, ибо реакции образования нитридов железа неэкзотермичны, а сами нитриды термически неустойчивы. Так, исследования показали, что если в азотируемый порошок ванадия добавлять порошок железа, то скорость горения такой смеси быстро снижается с ростом в ней концентрации железа. Содержание азота в продукте также постепенно уменьшается.
На рис. 1 представлена зависимость скорости горения феррованадия от концентрации в нем ванадия. Для сравнения приведена аналогичная зависимость для смесей порошков ванадия с железом. Видно, что при переходе от металлического ванадия к сплавам FeV80 и FeV60 скорость горения быстро снижается, причем на этом участке скорости горения сплавов V—Fe и смесей порошков V и Fe близки. Однако при дальнейшем уменьшении концентрации ванадия в сплаве при переходе к феррованадию FeV50 скорость горения резко возрастает (более чем вдвое). В то же время увеличение концентрации железа в смеси порошков с 40 до 45 % приводит к дальнейшему монотонному снижению скорости горения. Смесь порошков при массовом соотношении ванадия и железа 50:50 проазотировать в режиме горения не удается.
Рис. 1. Влияние содержания ванадия в феррованадии на скорость горения: 1 - сплавы феррованадия; 2 - смеси порошков ванадия и железа
По данным рентгенофазового анализа исходных сплавов феррованадий марок FeV80 и FeV60 имеет кристаллическую структуру α-фазы (твердый раствор железа в ванадии), а феррованадий марок FeV50 и FeV40 – σ-фазы (тетратональное интерметаллидное эквиатомное соединение VFe). В соответствии с диаграммой состояние V-Fe в интервале концентрации 35-55 % V при нагреве свыше 1100-1200˚С сплавы претерпевают фазовое превращение. Причем, переход σ-интерметаллида в α-твердый раствор происходит с очень большой скоростью. Резкое возрастание диффузионных процессов во время и непосредственно после фазового перестроения и является причиной неожиданного возрастания скорости горения σ-феррованадия по сравнению с α-сплавом.
На рисунке 2 приведены фотографии, полученные со шлифа образца с остановленным закалкой процессом горения. Измерение микротвердости непроазотированных частиц, непосредственно прилегающих к зоне горения (узкий слой образца толщиной 0,1 мм), в которой происходит интенсивное поглощение азота, позволило обнаружить резкое изменение их твердости. Частицы, находящиеся ближе к зоне горения, имеют меньшую микротвердость (~300 кг/мм2), что совпадает с микротвердостью α-феррованадия. Отдаленные от зоны горения частицы с более низкой температурой отличаются намного более высокой микротвердостью (~1400 кг/мм2), соответствующей исходному σ-феррованадию.
Рисунок 2 – Микроструктура зоны горения закаленного образца FeV50: 1 – σ-фаза; 2 – α-фаза
Послойный рентгенофазовый анализ подтвердил данные металлографических исследований образцов с остановленным фронтом горения. Так, если исходный феррованадий регистрируется как α-фаза, а конечный продукт - азотированный феррованадий - состоит из α-железа и δ-мононитрида ванадия, то между ними обнаруживается очень тонкий слой порошка, непосредственно прилегающий к исходному сплаву, который рентгенографически фиксируется как α-твердый раствор железа.
Таким образом, механизм ускоренного горения промышленных феррованадиевых сплавов со структурой σ- интерметаллида обусловлен фазовым переходом σ→α, происходящим в зоне прогрева по достижении соответствующей температуры.
При азотировании модельных феррованадиевых сплавов, было найдено, что поглощение азота сплавами обычно происходит в две стадии. Большая часть азота фиксируется сплавом в волне горения во время послойного азотирования. Остальная часть азота поглощается азотосодержащим полупродуктом после прохождения фронта послойного горения в результате объемного дореагирования. Для того, чтобы мог реализоваться двухстадийный режим процесса азотирования необходимо выполнение двух условий. Во-первых, непосредственно в волне горения степень превращения азотируемого металла (в данном случае ванадия) в нитрид не должна быть максимальной, т.е. должно оставаться горючее для его сгорания в объемном режиме. Во-вторых, азотосодержащий полупродукт, сформировавшийся за фронтом азотирования, должен сохранять высокую проницаемость (пористость), чтобы азот из окружающего образец пространства мог беспрепятственно поступать внутрь и фиксироваться там в виде соответствующих нитридов. Во многих случаях оба этих условия выполняются.
Для того, чтобы обнаружить стадийность поглощения азота при фильтрационном горении сплавов пользуются двумя приемами. В первом случае осуществляют горение в специальной СВС-установке, позволяющей непрерывно регистрировать изменение веса образца в течение всего процесса. На рис. 3 представлены кривые, полученные с использованием такой установки для промышленного феррованадия. Видим, что кривые изменения веса образцов с течением времени для сплавов FeV80 и FeV60 качественно отличаются от аналогичных зависимостей для сплавов FeV50 и FeV40. Гравиметрические кривые, относящиеся к σ- сплавам имеют излом, после которого масса образцов остается неизменной. Те же кривые, относящиеся к α- феррованадию (FeV80 и FeV60), излома не имеют. После линейного участка, соответствующего стадии послойного горения, кривые плавно стремятся к максимальному значению (объемное догорание). Таким образом, можно констатировать, что при получении азотированного феррованадия, состав которого лежит в пределах существования α-фазы (содержание ванадия более 55%), реализуется двухстадийный режим поглощения азота. На первой стадии в режиме послойного горения поглощается ≈ 75% N, оставшееся количество азота фиксируется в α-феррованадии в режиме объемного догорания. Сплав, по концентрации ванадия лежащий в пределах существования σ – фазы (35-55%), азотируется в одностадийном режиме. Весь азот, зафиксированный в интерметаллидном сплаве в виде мононитрида ванадия поглощается им на стадии послойного горения.
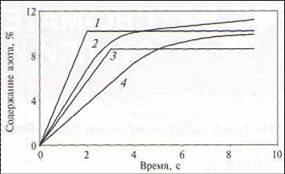
Рис. 3. Гравиметрические кривые азотирования феррованадия: 1 - FeV50; 2 - FeV80; 3 - FeV40; 4 - FeV60
Подтверждением различного механизма насыщения азотом α- и σ-феррованадия служат результаты, полученные другим способом, а именно послойным химическим анализом закаленных образцов. Путем резкого охлаждения недогоревших образцов горение останавливалось. Далее проводился их химический анализ с использованием метода Свельзаля. Для химанализа пробы брались из слоев, непосредственно прилегающих к фронту горения со стороны продуктов азотирования (готового азотированного феррованадия (на расстоянии ≈ 0,5 мм). Полученные результаты представлены на рис 4. Здесь кривая 1 - это расчетные значения максимально возможного содержания азота при условии полного превращения ванадия в стехиометрический нанонитрид. Кривые 2 и 3 это содержание азота в продуктах горения соответственно сплавов и смесей при медленном остывании образцов. Кривая 4 относится к концентрации азота в закаленных образцах. Сравнивая кривые 2 и 4 видим, что если для ванадия и α- феррованадия (сплавы с 78,8 и 59,2 % V) концентрация азота в закаленных образцах заметно ниже чем содержание его в медленно остывавших образцах, то для σ- феррованадия (сплавы с 52,4 и 41,6 % V) соответствующие концентрации практически совпадают. Таким образом, подтверждается вывод, сделанный из экспериментов по непрерывному взвешиванию образцов во время азотирования. При горении сплавов, по составу соответствующих σ- интерметаллиду, азот фиксируется в продукте в одну стадию непосредственно в зоне послойного горения. Если же азотируется феррованадий со структурой α- твердого раствора, то поглощение азота двухстадийное. Однако, несмотря на это, степень превращения ванадия в нитрид в σ- феррованадии выше, чем в α- феррованадии: 83 и 84 % для сплавов FeV50 и FeV40 и 68 и 79 % для сплавов FeV80 и FeV60. Для металлического ванадия эта величина еще меньше – 58%.

Рис. 4. Влияние содержания ванадия в феррованадии на степень азотирования: 1 - FeV50; 2 - FeV80; 3 - FeV40; 4 - FeV60
Температура горения при получении азотированного феррованадия была измерена микротермопарным методом с использованием вольфрам-рениевых термопар ВР5/ВР2. На рис 5-7 представлены типичные профили температур для α- и σ- феррованадия.
Рис. 5. Влияние давления азота на скорость горения (а) и степень азотирования (б) феррованадия (1-4 см. на рис. 3)
Рис. 6. Влияние дисперсности порошка на скорость горения (а) и степень азотирования (б) феррованадия (1-4 см. на рис. 3)
Рис. 7. Влияние пористости образцов на скорость горения (а) и степень азотирования (б) феррованадия (1-4 см. на рис. 3)
Температура в волне горения интерметаллидного сплава нарастает с очень большой скоростью и далее в течение продолжительного времени остается неизменной. Скорость повышения температуры горения α-феррованадия заметно меньше, однако при этом достигается более высокая температура. Измеренные в работе максимальные температуры горения азотированного феррованадия в зависимости от условий процесса изменяются в довольно широких пределах для сплава FeV80 от 1780 до 2060 ˚С, для FeV60 от 1630 до 1830 ˚С, для FeV50 от 1480 до 1560 ˚С и для FeV40 от 1420 до 1490 ˚С. Анализ полученных результатов показал, что в общем случае максимальные температуры хорошо корелируются с содержанием азота в продукте: чем больше азота поглощается сплавом, тем более высокий разогрев фиксируется при горении. Качественные различия температурных профилей свидетельствуют о различном механизме горения α- и σ-феррованадия: поглощение азота интерметаллидным сплавом происходит в одну стадию, а твердорастворным – в две.
Известно, что экономическая эффективность использования ванадия может возрасти в случае применения различных его комплексных сплавов, в том числе азотсодержащих (азотированного феррованадия). В настоящей работе исследуется возможность получения сложных азотированных ванадийсодержащих сплавов в комбинации с марганцем, ниобием и кремнием. Источниками этих компонентов служили порошки стандартных промышленных сплавов: феррониобия, марганца и ферросилиция. Несмотря на то, что теплоты образования нитридов кремния (Si3N4), ниобия (Nb6N) и марганца (Mn3N2) вполне сопоставимы с экзотермичностью нитридов ванадия, интенсивность их взаимодействия с азотом оказалась много меньше. Как видно на рис. 8, все три добавки снижают скорость горения феррованадия. Марганец и ниобий несколько уменьшают концентрацию азота в продуктах горения, а ферросилиций напротив значительно ее повышает. Таким образом, СВС-технология позволяет производить любые комплексные лигатуры, включающие V, Nb, Mn и/или Si с использованием в качестве сырья порошков стандартных ферросплавов на их основе. Концентрация азота близка к максимальным значениям, соответствующим выбранным составам.
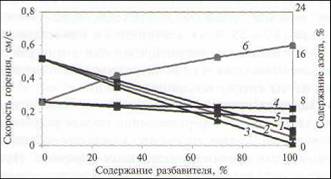
Рис. 8. Влияние разбавления ферросплавами на скорость горения (1-3) и степень азотирования феррованадия (4-6): 1 и 4 - FeNb; 2 и 5 - Mn; 3 и 6 - FeSi
Результаты лабораторных исследований, полученные с использованием промышленных феррованадиевых сплавов были использованны при создании технологии производства азотированного феррованадия на больших установках с рабочим объемом 0,15 м3. Скорость горения в таких промышленных СВС-реакторах определяется по показаниям расходомера, установленного на входе в установку. После инициирования процесса горения путем подачи электроимпульса на зажигающее устройство реактора расход азота резко возрастает, быстро достигая постоянного значения. Процесс получения азотированного феррованадия с постоянным расходом соответствует стадии послойного стационарного горения. Окончание этой стадии фиксируется расходомером также по резкому изменению скорости поглощения азота. Причем при азотировании σ-феррованадия расход азота снижается практически до нуля, что является дополнительным свидетельством об отсутствии стадии дореагирования в объемном режиме. В случае азотирования α-феррованадия после момента быстрого снижения скорости поглощения азота, фиксируемого расходомером, насыщение азотом сплава продолжается при более низком и постоянно уменьшающемся его потреблении. Измеренные таким образом скорости горения феррованадия в промышленной установке оказались близкими к результатам, полученным при азотировании на лабораторной установке. Так, например, продолжительность горения сплава марки FeV50 при давлении в 12 МПа составила ≈ 5-8 мин, что соответствует скорости послойного горения ≈ 0,2-0,3 см/сек. Интенсивность поглощения азота феррованадием составила ≈ 0,1 м3/с. Концентрация азота в готовом азотированном феррованадии зависит от марки исходного сплава, давления азота в СВС-реакторе во время горения, дисперсности порошка и ряда других факторов и может изменяться в пределах от 8 до 16 %.
Для достижения в продуктах горения максимально возможных (предельных) концентраций азота в работе был использован традиционный в этих случаях прием. Для снижения экзотермичности шихты в нее обычно добавляют продукты реакции, которые, во-первых, снижают температуру процесса, а с другой стороны препятствуют коагуляции частиц во фронте горения и снижению проницаемости после его прохождения, создавая тем самым условия для максимального превращения металла в нитрид при доазотировании. Влияние разбавления исходной шихты продуктами реакции было исследовано на примере горения высокопроцентного феррованадия марки FeV80 и FeV60. На рис. 9 представлена зависимость содержания азота в готовом азотированном феррованадии от количества в исходной смеси продуктов азотирования. В качестве разбавителя использовались порошки азотированного феррованадия, полученные из тех же самых ферросплавов. Дисперсия всех порошков была одинаковой: 0,04 мм порошок нитрида феррованадия, синтезированного из сплава FeV80 содержал 12,1 % N, а из смеси FeV60 – 10,9 % N. Из рисунка видим, что предельная концентрация азота в FeV80 достигается при добавлении в шихту 30 % продукта, а в FeV60 – 15 %. Скорость горения смесей при их разбавлении конечным продуктом быстро снижается при возрастании его концентрации.
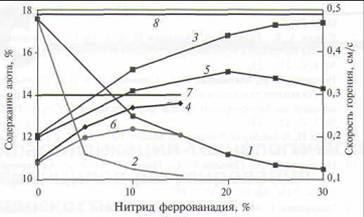
Рис. 8. Влияние разбавления продуктом на скорость горения (1 и 2) и степень азотирования (3-6) феррованадия: 1, 3, 5 - FeV80 (FeVN80; 2, 4, 6 - FeV60 (FeVN60); 3 и 4 - общее содержание азота при горении; 7 и 8 - предельное содержание азота для FeV60 (7) и FeV80 (8)
Для промышленного использования были разработаны два типа азотированного феррованадия: плавленый и спеченный. Первый предназначен для традиционного кускового легирования сталей в ковше либо непосредственно в печном агрегате. Второй сплав эффективен при использовании в качестве наполнителя порошковой проволоки и предназначен для доводки концентрации азота пред разливкой. Сырьем для синтеза плавленого нитрида феррованадия служат сплавы марок FeV40 и FeV50 по ГОСТ 2730, а для спеченного – сплавы марок FeV80. В табл. 2 приведены основные характеристики плавленого азотированного феррованадия. Здесь же для сравнения представлены те же данные для сплава типа NITROVAN и печного азотированного феррованадия по ТУ 14-5-122-80.
Таблица 2. Состав и свойства азотсодержащих сплавов ванадия
Показатель |
Печной нитрид феррованадия FeV40; FeV50 |
Сплав типа Nitrovan V2O5, V2O3, C |
СВС-нитрид феррованадия плавленый FeV40; FeV50 |
Состав, %: |
ванадий |
> 34 |
76-78 |
44-48 |
азот |
4-10 |
10-18 |
9-11 |
углерод |
< 0,5 |
1-10 |
< 0,5 |
марганец |
1-4 |
- |
0,5-4 |
примеси |
По ГОСТ 27130 |
Кислород до 1,5 |
По ГОСТ 27130 |
Соотношение N:V (по массе) |
1:6 |
1:5 |
1:5 |
Фазовый состав |
V2N, VN, α-Fe |
VCN |
VN, α-Fe(Mn) |
Плотность, г/см3 |
4,0-4,5 |
3,0 |
6,0-6,5 |
Плотность насыпная, г/см3 |
2,2 |
1,6 |
3,5 |
Пористость, %, общая/открытая |
40/40 |
50/50 |
5/0 |
Размер кусков, мм |
< 100 |
33x28x23 |
30-60 |
Количество порошообразных фракций, % |
до 10 |
до 5 |
отсутствуют |
Прочность на сжатие, МПа |
< 10 |
< 10 |
> 100 |
Температура плавления, oC |
< 1450 |
> 2400 |
< 1450 |
Степень усвоения азота, % |
> 50 |
>60 |
>85 |
Степень усвоения ванадия, % |
> 80 |
> 75 |
>95 |
Плавленый нитрид феррованадия был использован при выплавке различных марок высокопрочных низколегированных сталей, а также рельсовой и быстрорежущей стали. Степень усвоения азота составила 86-98 %. Следует обратить внимание на то, что степень усвоения самого ванадия оказалась также исключительно высокой и достигла 95 % и более.
Таким образом, новая технология производства азотированного феррованадия, основанная на принципах металлургического СВС–процесса, позволяет получать продукцию с уникальным сочетанием высокой плотности, характерной для плавленых лигатур, с максимальным содержанием азота, характерным для спеченных легирующих материалов. Кроме того, благодаря концентрационной структуре нового сплава (αFe – δVN) плавленый азотированный феррованадий имеет высокую прочность. Вследствие этого полностью исключается разрушение сплава при различных технологических операциях, а также исключается образование не только порошкообразных (пылевидных) частиц, но и любых кусков менее 10 мм.
Опубликовано в журнале "Сталь". № 11. 2009 г.
Производимый ООО "НТПФ "Эталон"
Другие материалы по теме