Страница для печатиМ. X. Зиатдинов1, И. М. Шатохин2
1 - Томский государственный университет (г. Томск, Россия)
2 - ООО "НТПФ "Эталон" (г. Магнитогорск. Россия)
В 1970-е годы на рынке появился новый огнеупорный материал, названный нитридом ферросилиция, так как сырьем для его производства служил порошок высокопроцентного ферросилиция, который насыщали азотом в высокотемпературной печи сопротивления. Основу азотированного таким образом ферросплава составляет нитрид кремния Si3N4 (70 - 80 %), кроме того, в нем содержатся железо и/или его силициды, а также примесные элементы, типичные для стандартного ферросилиция с 75 % Si. Новый материал был предназначен для применения в неформованных огнеупорных смесях в качестве упрочняющей добавки. Леточные и желобные массы для доменного производства, изготовленные с добавлением нитрида ферросилиция, показали высокую эффективность и получили широкое распространение, особенно в Японии.
Содержание нитрида ферросилиция в неформованных огнеупорах может изменяться в широких пределах — от 5 до 30 % в зависимости от условий, в которых они эксплуатируются. В частности, на качественный состав леточных и желобных масс влияют размер доменной печи и режим, при котором выпускают чугун и шлак. Однако в любом случае благодаря введению азотированного ферросилиция повышаются прочность и износостойкость огнеупорных масс при высоких температурах, увеличиваются термоустойчивость и стойкость к окислению, уменьшается коэффициент термического расширения при одновременном росте теплопроводности. Важно и то, что стойкость огнеупоров повышается по отношению как к чугуну, так и к шлакам. Кроме того, такие огнеупорные массы не подвержены усадке при повторном нагреве. Максимальная эффективность леточных масс с нитридом ферросилиция достигается при их использовании для закрытия леток печей с большими объемами рабочего пространства.
Несколько позже нитрид ферросилиция начали применять как эффективный легирующий материал при выплавке коррозионно-стойких сталей с повышенным содержанием азота по технологии электрошлакового переплава под давлением. Благодаря высокому содержанию азота в азотированном ферросилиции, использованном для легирования (25 - 30 % N), и сравнительно низкой концентрации в нем углерода появилась возможность выплавлять высокопрочный металл с максимальным количеством азота (более 1,0 %). При этом расход легирующего материала оказался минимальным при сравнительно высокой степени усвоения азота расплавом. По сравнению с традиционно применяемыми для легирования азотом марганцевыми и хромистыми сплавами потребление азотсодержащей лигатуры уменьшилось в несколько раз.
Несмотря на то, что к настоящему времени в мире накоплен большой положительный опыт использования азотированного ферросилиция, для отечественных предприятий он оказался новым материалом. Лишь в последние годы ситуация стала меняться и его начали успешно осваивать российские металлурги после того, как на производственных площадях НТПФ "Эталон" (Магнитогорск) была создана единственная в своем роде промышленная технология получения продукции на основе тугоплавких неорганических соединений. Уникальность нового производства заключается в том, что впервые было освоено многотоннажное производство, основанное на принципах метода самораспространяющегося высокотемпературного синтеза (СВС). В сочетании с такими преимуществами СВС-технологии как отсутствие потребления электроэнергии, быстротечность процесса в экстремальных условиях повышенного давления и максимальных температур, а также простотой оборудования, найден новый подход к выбору сырьевых материалов для синтеза горением. Взамен дорогих порошков чистых металлов и дефицитных химреактивов, традиционных для СВС-процесса, используются ферросплавы, раскислители и другие, более дешевые продукты металлургического производства. Благодаря этому впервые удалось обеспечить массовому производству, основанному на методе СВС, высокую экономическую эффективность.
Следует отметить, что СВС-технология, кроме того, позволяет производить продукцию более высокого качества с новым сочетанием эксплуатационных свойств по сравнению с обычными печными технологиями. Например, ранее, но только выбором в качестве сырья сплава ванадий - железо с определенным соотношением компонентов для осуществления СВС- процесса, удалось создать новый легирующий сплав — плавленый азотированный феррованадий с большой плотностью (~ 6,5 г/см3) и максимальной концентрацией азота (10 - 12 %). Слиток такого материала, представляющего собой композицию Fe-VN, невозможно получить традиционным печным способом. При использовании СВС-нитрида феррованадия обеспечивается практически полное усвоение азота расплавом и гарантируется получение в стали узких концентрационных пределов по азоту и ванадию. Улучшение эксплуатационных свойств новых материалов достигается тем, что синтез горением происходит в условиях, сочетающих высокое давление реагирующего газа с высокой температурой самого процесса. Так, при получении азотированного ферросилиция температура в зоне горения составляет ~ 2000 °С, а давление в рабочем пространстве СВС-реактора — 10 МПа.
Освоение СВС-нитрида ферросилиция в России началось с его успешного применения в качестве лигатуры при выплавке трансформаторной стали с нитридным вариантом ингибирования. В конвертерном цехе ОАО ММК применение нового легирующего материала взамен обычного азотсодержащего феррохрома позволило практически до 100 % повысить выход стали по концентрации азота. В НТПФ "Эталон" специально для выплавки трансформаторной азотсодержащей стали была разработана комбинированная технология легирования металла азотом. В соответствии с новым способом предварительное насыщение расплава азотом в виде кускового нитрида ферросилиция осуществляется в ковше при разливке с получением в стали около 0,006 % N. Окончательно состав по азоту корректируется также азотированным ферросилицием, который предварительно измельчается в порошок, упаковывается в проволоку и вводится во время внепечной обработки с получением в металле 0,009 - 0,012 % N.
Печной азотированный ферросилиций зарубежного производства содержит обычно около 30 % N. Причем один и тот же материал применяется как для легирования стали азотом, так и в качестве упрочняющей добавки в неформованных огнеупорах. СВС-азотированный ферросилиций, предназначенный для легирования стали, содержит меньше азота — 18-23 %. Переход на порошковую проволоку, в наполнителе которой сокращено содержание азота, позволил повысить степень его усвоения и стабилизировать выплавку металла с заданными узкими концентрационными пределами азота. Кроме того, специально для кускового легирования в ковше были разработаны композиции азотированного ферросилиция с более высокими плотностью и прочностью. Плотность кускового СВС-нитрида ферросилиция превышает плотность традиционного печного продукта в 1,5 - 2,0 раза. Прочность самих кусков увеличена в несколько раз, благодаря этому удалось практически полностью исключить пылеобразование при использовании нового материала, максимально увеличив при этом степень усвоения азота сталью.
Следует также отметить, что для кускового легирования в ковше была предложена простая оригинальная технология, не только обеспечивающая высокое и стабильное усвоение азота сталью, но и позволившая дополнительно на 5 - 10 % сократить общий расход кремния вследствие его более полного усвоения из обычного неазотированного ферросилиция.
В отличие от СВС-азотированного ферросилиция, применяемого для азотирования стали, в композициях, предназначенных для использования в качестве добавок в неформованные огнеупоры, концентрация азота более высокая. НТПФ "Эталон" разработала нитрид ферросилиция с повышенным содержанием азота при одновременном уменьшении концентрации железа. Более высокая концентрация нитрида кремния обеспечивается как выбором соответствующего сырья, так и использованием условий процесса, гарантирующих образование продукта с максимальным количеством азота. Исследования леточных и желобных масс, содержащих СВС-нитрид ферросилиция, показали, что концентрация нитрида кремния в них должна быть не менее 75 %. После отработки технологии и проведения промышленных испытаний в течение 2006 г., в настоящее время доменный цех ММК полностью перешел на использование безводных леточных масс, в состав которых включен азотированный ферросилиций, полученный СВС-методом. Освоение новых огнеупоров обеспечило большую продолжительность выпуска чугуна при одновременном увеличении количества выпущенных продуктов плавки. Кроме того, заметно улучшились условия труда доменщиков. Следует отметить, что свойства леточных масс с СВС-нитридом ферросилиция улучшились по сравнению не только с традиционными безнитридными огнеупорами, но и с массами, содержащими обычный печной нитрид зарубежного производства.
Основу СВС-нитрида ферросилиция составляет нитрид кремния, который при использовании композиции в качестве легирующего материала служит источником азота. Если азотированный ферросилиций вводится в огнеупорные массы, то Si3N4 оказывает упрочняющее воздействие. Чистый нитрид кремния почти на 40 % состоит из азота (стехиометрическое содержание 39,94 % N), при этом он практически не имеет области гомогенности. При нормальном давлении (0,1 МПа) нитрид кремния разлагается без плавления при 1900 °С. Рост давления приводит к повышению температурной устойчивости Si3N4. При контакте со стальным расплавом нитрид кремния активно взаимодействует с ним, выделяя азот. Образование нитрида кремния сопровождается выделением большого количества тепла:
3Si + 2N2 --> Si3N4 + 75,18 кДж/моль.
Высокая экзотермичность реакции дает возможность реализовывать синтез нитрида кремния в режиме самоподдерживающегося горения. Расчетная адиабатическая температура горения кремния в азоте исключительно высока и превышает 4000 °С, однако она может быть достигнута лишь при условии, что весь кремний превращается в нитрид, а теплопотери в окружающую среду отсутствуют. Предполагается также, что нет сублимации продуктов синтеза. На практике эти условия очень сложно воспроизвести, поэтому наблюдаемые в экспериментах величины максимального разогрева при горении кремния в азоте оказались намного меньше — 1900 - 2200 °С.
Адиабатическая температура горения ферросилиция в азоте будет ниже, чем расчетная температура горения кремния, так как тепловой эффект взаимодействия сплава с азотом заведомо меньше, чем экзотермичность чистого металла. Основная причина этого — наличие в ферросилиции значительного количества железа, которое, в отличие от кремния, реагирует с азотом практически без тепловыделения, а образовавшиеся при этом нитриды термически неустойчивы. Другая причина меньшей экзотермичности ферросилиция состоит в том, что кремний и железо в нем связаны в термически устойчивые силициды, на разложение которых необходимо затратить значительное количество энергии. Температура горения рассчитывается из условия равенства энтальпий исходных материалов при начальной температуре (Tо) и продуктов синтеза при температуре горения (Тг). Таким образом, все тепло, выделившееся при образовании Si3N4, идет на нагрев продуктов, т. е. нитрида кремния и железа:
μ[H(Tг) - H(To)]Si3N4 + (1 - μ)[H(Tг) - H(To)]Fe = μQ,
где О — тепловой эффект образования Si3N4; μ — доля нитрида кремния в продукте; H(Tо,), H(Тг) — энтальпии продуктов сгорания при Tо и Tг
Рассчитанная по этой формуле температура горения оказалась достаточно высокой для сплавов с различным содержанием кремния. Так, даже для ферросилиция с 45 % Si расчетная температура горения достигает ~ 2500 °С. Следовательно, имеются реальные термодинамические предпосылки для успешного осуществления СВ-синтеза азотированного ферросилиция в широком диапазоне изменения состава исходного сплава. Действительно, экспериментальные исследования подтвердили, что горение можно реализовать для всех марок ферросплава, содержащего свыше 40 % Si.
Закономерности процесса получения азотированного ферросилиция оказались во многом схожими с горением металлического кремния. Так, при его азотировании столкнулись с тем, что в продуктах сгорания остается много непрореагировавшего кремния, вследствие чего была сравнительно низкая температура горения. Такая неполнота превращения кремния в нитрид обусловлена низкой температурой плавления самого кремния (1415 °С) и относительно невысокой температурой диссоциации его нитрида. Степень превращения кремния в нитрид, полученная в экспериментах, составляла 50 - 60 %. Температура плавления сплавов системы Fe - Si еще ниже, чем кремния. В сплавах, содержащих 40 - 80 % Si, жидкая фаза образуется уже при температуре выше 1210 °С. Следовательно, процессы, связанные с плавлением исходного материала при горении ферросилиция, могут проявиться более ярко.
Известно, что азотирование металлических порошков, в том числе и кремния, происходит по механизму фильтрационного горения. Особенность фильтрационного варианта СВС-процесса в том, что газообразный реагент доставляется в зону горения путем фильтрации через пористую среду, образованную металлическим компонентом. При получении азотированного ферросилиция фильтрация возникает и постоянно поддерживается разностью давлений азота во внешней среде и зоне реакции. Давление в зоне горения непрерывно падает в результате интенсивного поглощения сплавом азота при высокой температуре. Необходимость фильтрационной доставки азота в зону горения извне возникает потому, что в обычных условиях (при нормальном атмосферном давлении и комнатной температуре) количество его в порах порошкообразного ферросилиция очень мало и явно недостаточно для поддержания процесса азотирования в самоподдерживающемся режиме горения. Более того, расчеты показывают, что внутрипорового азота недостаточно для азотирования ферросилиция и при повышенном давлении. Например, при давлении 10 МПа азота, содержащегося внутри порошка, достаточно лишь для связывания в нитрид 1 — 5 % Si в зависимости от состава ферросилиция и пористости порошковой шихты. Такая степень азотирования может дать повышение температуры в системе Fe - Si - N2 не более чем на 200 - 500 °С, что не только явно недостаточно для поддержания процесса в самораспространяющемся режиме, но и исключает возможность химического взаимодействия.
Для фильтрационного типа горения характерна сильная зависимость параметров процесса от характеристик реагирующей системы, определяющих условия фильтрации, а именно давления азота, дисперсности порошка ферросилиция, пористости и геометрических размеров шихты. Кроме того, на параметры горения ферросилиция в азоте будут влиять исходные условия, определяющие тепловой баланс в системе, в частности наличие инертных компонентов и их количество, величина начальной температуры ингредиентов, введение активирующих добавок, возможность плавления исходных порошков и/или продуктов реакции.
На рис. 1 приведены зависимости, отражающие влияние концентрации кремния в исходном ферросилиции и давления азота на скорость горения, степень азотирования сплава и максимальную температуру, развивающуюся в волне реакции. Данные получены по результатам исследования процесса СВС на экспериментальной установке объемом 15 л. Окна из кварцевого стекла позволяют визуально наблюдать за процессом горения и фиксировать режим распространения волны горения на видеоаппаратуре. Лабораторная установка снабжена также системой непрерывного измерения температуры горения с помощью термопар и записью температурного профиля на компьютер. Для азотирования используются порошки ферросилиция марок (по ГОСТ 1415-93) ФС90, ФС75, ФС65 и ФС45 с содержанием кремния в них соответственно 89,9, 79,4, 68,1 и 48,25 %, углерода - 0,06, 0,08, 0,07 и 0,2.3 % и стандартным содержанием других примесей. Во всех случаях размер частиц порошков не превышает 0,08 мм.
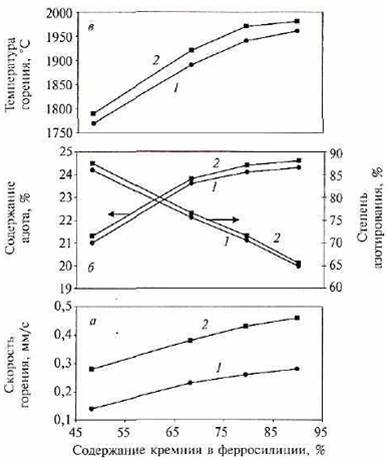
Рис. 1. Влияние содержания кремния в ферросилиции на скорость горения (а), степень азотирования (б) и температуру горения (в); 1 - PN2 - 3 МПа; 2 - PN2 - 7 МПа
В соответствии с диаграммой состояния Fe — Si сплавы с высокой концентрацией кремния относятся к двухфазным и состоят из кремния и дисилицида железа FeSi. Причем чем больше в сплаве кремния, тем в большем количестве выделяется он в свободном виде, что подтверждается рентгенофазовым анализом исходных порошков ферросилиция. Так, если в сплаве ФС65 доля свободного кремния не превышает 25 %, то в сплаве ФС90 она увеличивается до 80 — 85 %. Низкокремнистый ФС45 также имеет двухфазную структуру: примерно 70 % — FeSi2, остальное; — силицид FeSi.
Как и следовало ожидать, с увеличением в исходном составе доли кремния усиливается интенсивность его взаимодействия с азотом, что проявляется в значительном повышении скорости горения, одновременно с ней возрастает концентрация азота в продуктах - азотированном ферросилиции. В то же время, степень азотирования кремния в сплавах сокращается по мере уменьшения в них количества железа. Так, несмотря на относительно низкое содержание азота в ферросилиции ФС45, степень превращения в нем кремния в нитрид максимальна и достигает почти 90 %, в то же время для сплава с 90 % Si она падает до 65 %. Характер зависимостей скорости горения, содержания азота, степени азотирования и температуры горения от доли кремния в ферросилиции не зависит от величины давления азота. Рост давления сильно влияет на скорость горения, но при этом практически не изменяется степень азотирования сплавов. Температура горения при повышении давления несколько поднимается.
Рентгенофазовый анализ продуктов сгорания ферросилиция в азоте - азотированного ферросилиция - показал, что во всем исследованном диапазоне изменения исходных параметров основную фазу в них составляет нитрид кремния β-модификации. Заметных количеств α-нитрида кремния не обнаруживается. Это, вероятно, связано с тем, что нитрид с α-структурой устойчив лишь до - 1400 °С и при более высокой температуре необратимо переходит в β-модификацию. Температура горения ферросилиция в азоте составляет более 1750 °С при всех исследованных начальных условиях, поэтому образование α-Si3N4 становится маловероятным. На рис. 2 приведены типичные рентгенограммы продуктов азотирования сплавов ФС45 и ФС75.
Рис. 2. Типичные рентгенограммы продуктов азотирования ферросилиция ФС45 (а) и ФС75 (б); 1 - Fe; 2 - FeSi; 3 - Si3N4
Ранее при изучении процесса азотирования феррованадия в режиме саморегулируемого горения было обнаружено, что в зависимости от агрегатного состояния продуктов за волной горения возможна стадийность поглощения азота. Если доля жидкости в продукте сгорания велика, то непосредственно за волной горения образуется газонепроницаемая структура. В том случае, когда в продуктах сгорания большую часть составляют тугоплавкие компоненты, газопроницаемость материала сохраняется, а поглощение азота продолжается и за волной реакции в режиме объемного догорания. Следует отметить, что необходимым условием для возникновения стадии дореагирования наряду с сохранением проницаемой структуры является неполнота превращения непосредственно в волне горения. В большинстве случаев это условие на практике выполняется, так как в реальном процессе размеры частиц порошков значительно больше тех размеров, при которых горение будет происходить в кинетическом режиме, т. е. в условиях, исключающих диффузионные и фильтрационные препятствия для химического взаимодействия.
Анализ структуры образцов азотированного ферросилиция показал, что во всех случаях они сохраняют значительную проницаемость. Пористость продуктов сгорания составляет 35-35 % в зависимости от условий синтеза. При наличии столь высокой пористости за фронтом горения становится возможным интенсивное поглощение азота. Для определения вклада такого доазотирования в общее содержание азота в продукте горения прерывали, резко сбрасывали давление и из рабочего объема реактора и заполняя его аргоном. Химический анализ закаленных таким образом образцов показал, что в результате дореагирования значительно увеличивается содержание в них азота. Доля азота, поглощенного после прохождения волны послойного горения в результате объемного догорания, может достигать 30 %. Большой вклад стадии доазотирования в общее количество азота объясняется в частности слабой зависимостью его содержание в продукте от давления. На рис. 3 показана типичная структура азотированного ферросилиция.
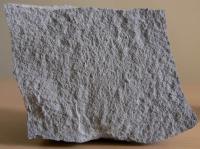
Рис. 3. Макроструктура СВС-нитрида ферросилиция
Важно то, что азот исключительно равномерно распределен по объему продукта. Фактически азотированный ферросилиций представляет собой композиционный материал, состоящий преимущественно из нитрида кремния. Своеобразной связкой в такой композиции служат железо и его силициды. Причем при высоком содержании в продукте азота возрастает доля свободного железа, а при снижении степени азотирования — количество силицидов. Вследствие того, что плотность Si3N4 (3,19 г/см3) намного меньше, чем железа и его силицидов, объемная доля нитрида кремния в продукте всегда очень высока (80 - 95 %).
Для промышленного производства азотированного ферросилиция и других СВС-материалов на НТПФ "Эталон" разработан СВС-реактор рабочим объемом 0,15 м3. Это толстостенный металлический сосуд с системами охлаждения, ввода и выпуска газа, зажигания и герметизации. Благодаря оригинальному устройству реактора с системой ускоренного охлаждения впервые удалось реализовать в промышленном масштабе СВС-технологию с рабочей температурой до 2200 °С при единовременной загрузке шихты до 0,3 т. Новая система герметизации позволяет надежно и безопасно осуществлять синтез в фильтрационном режиме горения при давлении азота до 15 МПа. При этом к минимуму было сведено время, затрачиваемое на открывание и герметизацию установки. Цех по производству нитрида ферросилиция и других СВС-материалов включает участки дробления и тонкого помола, сушки и загрузки тиглей, синтеза, диспетчерскую и центральный пульт управления, лаборатории входного контроля сырья и анализа продукции, а также склад исходных материалов и готовых продуктов. На участке синтеза расположены 20 реакторов СВС, общая площадь цеха составляет ~ 3000 м3. Новый цех имеет возможность производить в сутки до 10 т различной продукции. Универсальная конструкция СВС-реакторов позволяет изготавливать широкий спектр различных композиций на основе тугоплавких неорганических соединений нитридов, боридов, карбидов, сульфидов и др. Причем синтез можно осуществлять в атмосфере как реагирующего газа (азота), так и аргона или в вакууме.
В таблице приведены составы азотированного ферросилиция, производимого и поставляемого НТПФ "Эталон". Композиции продукции марок ФСН35 и ФСНЗО предназначены для огнеупорной промышленности. С использованием нитрид ферросилиция этих марок ОАО "Спецремстрой" (г. Магнитогорск) производит безводную леточную массу типа SiO2 – Al2O3 - SiC - С. Для легирования используются в основном композиции ФСН20 и ФСН15, обеспечивающие высокое и стабильное усвоение азота сталью.
Таблица 1. Химические составы азотированного ферросилиция производства НТПФ "Эталон"
Таким образом, рассмотрены результаты исследований, разработки и промышленного освоения НТПФ "Эталон" СВС-технологии производства нового материала — азотированного ферросилиция и создания первого в России многотоннажного производства материалов на основе тугоплавких неорганических соединений для металлургии.
NITRO-FESIL®, производимый ООО "НТПФ "Эталон":
Другие материалы по теме