Страница для печатиМ. X. Зиатдинов1, И. М. Шатохин2
1 - Томский государственный университет (г. Томск, Россия)
2 - ООО "НТПФ "Эталон" (г. Магнитогорск. Россия)
Азотированный феррохром или нитрид феррохрома является в настоящее время практически единственным легирующим материалом, используемым для выплавки нержавеющих азотсодержащих сталей. Производство азотированного феррохрома появилось в тридцатые годы прошлого столетия и было вызвано необходимостью введения в хромистые стали повышенного содержания азота. В первых работах, посвященных использованию азотирующих легирующих сплавов хрома, наблюдали улучшения структуры полученных слитков сталей типа «фуродит» (24-28 % Cr, ~0,25 % N) вследствие подавления в них транскристаллизации. Начавшаяся в те годы активная милитаризация ведущих экономик мира и жесткое разделение стран по сферам влияния привели к острому дефициту сырья для производства качественной стали, включая нержавеющую. Особо остро стояла проблема обеспечения никелем. Активный поиск альтернативы ему послужил мощным толчком к созданию азотсодержащих нержавеющих сталей. Азотное легирование позволило значительно сократить, а в ряде случаев и полностью отказаться от использования никеля. Здесь использовалось уникальное свойство азота как сильнейшего стабилизатора аустенита. По аустенитообразующей способности 0,1 % N эквивалентно ~2,0 % никеля. При этом азот, в противоположность углероду, также сильно расширяющему гамма-область, не снижает коррозионной стойкости стали. Более того, обнаружилось, что введением азота можно значительно повысить прочностные характеристики стали при сохранении ее пластичности.
Азот в обычных условиях это газ с практически неограниченными запасами в природе. Он доступен всем, не знает национальных границ, экологически безопасен. «Добыча» азота хорошо освоенный недорогой процесс, не сопровождающийся созданием каких либо отходов. Легировать сталь можно либо непосредственно природным газообразным азотом, либо использовать искусственные его носители в виде химических соединений или сплавов. С позиций современного сталеплавильного производства, когда основные операции по облагораживанию металла осуществляются при внепечной обработке, на первый взгляд представляется наиболее эффективным использование первого варианта азотирования. И действительно, в ряде случаев обработка стального расплава газообразным азотом дает положительные результаты. Однако у такой технологии есть и существенные недостатки. Это и невозможность достижения максимальных концентраций азота, и нестабильность усвоения азота, зависящая от большого количества технологических факторов и часто неприемлемо большая продолжительность продувки, ведущая к переохлаждению металла и т.д. Поэтому на практике чаще используют комбинированный способ: обработку расплава газообразным азотом дополняют введением твердых азотоносителей. В последнее время для этих целей всё чаще используют порошковую проволоку, наполнителем которой являются различные азотсодержащие соединения. Так как порошковая проволока вводится в сталь на заключительной стадии её производства, то количество её должно быть минимальным, а наполнитель содержать максимальное количество азота.
В настоящее время азотированный феррохром используют для выплавки большого класса нержавеющих сталей. Наиболее устоявшимися является выплавка аустенитных нержавеющих сталей с Cr-Mn и Cr-Mn-Ni основами. Различные варианты этих сталей стандартизированы в большинстве промышленно развитых стран. Широко распространенными и массовыми являются так называемые стали «серии 200» (например, UNS20100, UNS20200, UNS20500 и т.д.) Стали этих марок впервые появились в пятидесятых годах и быстро завоевали рынок США. В настоящее время наибольшее количество азотсодержащих нержавеющих сталей выплавляется в Китае и Индии, т.е. странах с наиболее динамично развивающейся металлургией. Доля азотсодержащих нержавеющих сталей в мире постоянно увеличивается и оценивается сейчас примерно в 10% от общего объема выплавки. В то же время в Азии эта доля достигает ~20 %. Хромомарганцевые азотсодержащие стали применяют в строительстве, транспорте, химической и пищевой промышленности, из них делают детали автомобилей и бытовой техники, а также посуду.
Кроме сталей 200-ой серии, которые являются массовыми, с широким спектром применения разработаны и используются высокоазотистые стали с узкоспециальным назначением. Из-за своих уникальных свойств они стали буквально безальтернативными. Яркими примерами таких сталей являются высокоазотированная сталь марки 08-12Х18АГ18 c ~0,5 % N, предназначенная для изготовления бандажных колец турбогенераторов, а также жаропрочная сталь 55Х21Г9АН4 с 0,3-0,6 % N, из которой делают клапаны двигателей автомобильной техники. Сюда же можно добавить стали для работы в криогенных условиях и стали, устойчивые в морской воде. Фактически только легированием азотом можно достичь одновременного повышения прочности, вязкости и коррозионной стойкости металла.
Азот реагирует с хромом и его сплавами только при высокой температуре, поэтому все современные способы азотирования основаны на различных вариантах печной технологии. Известна попытка производить азотсодержащий сплав хрома путем внепечного металлотермического восстановления. Однако эта технология не прижилась, т.к. она оказалась очень затратной, а получаемый продукт отличался низкой концентрацией азота – чуть более 1 %. При печной технологии азотирование может происходить при различных температурных режимах, которые определяют качество продукта. Если процесс осуществляют при температуре ниже температуры плавления феррохрома, то реализуется твердофазный механизм азотирования с образованием спеченного ферросплава либо порошка. Если же азотируется расплав, то реализуется жидкофазное азотирование и образуется литой азотированный феррохром. В первом случае максимально возможное количество азота в продукте определяется содержанием его в нитридах хрома, а во втором – растворимостью азота в хромистом расплаве.
Общие требования, которые сложились к настоящему времени за более чем 70-летнюю историю эксплуатации азотсодержащих легирующих сплавов, сводятся к следующему. Заданную марочным составом концентрацию азота стремятся стабильно достигать при минимальным расходе лигатуры, не привнося при этом в сталь заметных количеств нежелательных примесей. На практике это сводится к тому, что применяют более концентрированные по азоту и более чистые по примесям сплавы, а во время легирования стремятся достигать максимальную степень усвоения азота. Немаловажным является и то, чтобы сама технология производства таких сплавов была экономически эффективной. Если концентрация азота в легирующем материале определяется применяемой для его производства технологией, то на степень усвоения азота влияет множество факторов: и способ введения лигатуры в расплав, и наличие примесей, влияющих на растворимость азота, и марочный состав стали и т.д.
Со времени начала массового производства азотированного феррохрома в 50-е годы общей тенденцией являются постоянное повышение в нем концентрации азота и снижение количества углерода и других примесей. Это отражается как в нормативных документах на продукцию, так и в конкретных составах производимых лигатур. Например, если в предыдущем стандарте на азотированный феррохром ГОСТ 4757-49 была предусмотрена только одна марка сплава Хрн1 c ~1 % N, то в ныне действующем уже 8 марок с минимальным содержанием азота от 1 до 8 %.
В настоящее время в мире господствует вакуумтермическая технология производства азотированного феррохрома с получением высокоазотированного спеченного продукта. Иногда такой продукт переплавляют с получением высокоплотного слитка, но уже с низким содержанием азота. Сырьем для азотирования служит либо непосредственно низкоуглеродистый феррохром, либо феррохром углеродистый. В последнем случае перед насыщением сплава азотом его подвергают обезуглероживанию. В США для этих целей был приспособлен классический симплекс-процесс. На начальном этапе спеченная продукция содержала 2-5 % N, из которой после переплавки получали плавленую продукцию с 0,75-2,0 % N (Journal of Metals, 1956, V.8 N5, p.623). В настоящее время концентрация азота в азотированном симплекс-феррохроме составляет ~7,5 % (по данным компании ERAMET COMILOG). В таблице 1 представлена информация по некоторым составам азотированного феррохрома, производимым в различных странах.
Таблица 1. Примерный состав азотированного феррохрома*
Фирма-прозиводитель |
N |
Cr |
C |
Si |
P |
S |
Примечание |
Eramet Comilog, США |
6,5 |
64,0 |
0,05 |
2,0 |
0,03 |
0,03 |
Simplex, Гранулы 2х2х1 дюймов |
JPE Material Co. LTD, Япония |
6,0 |
52-62 |
0,20 |
1,0 |
0,04 |
0,03 |
Спеченный |
3,3 |
62 |
0,20 |
1,0 |
0,04 |
0,03 |
Переплавленный |
EWW Gmbh, Германия |
9 |
62-68 |
0,1 |
1,0 |
0,03 |
0,02 |
Порошок < 0,315 мм |
Nitrocor, Мексика |
10 |
60 |
0,1 |
1,5 |
0,04 |
- |
Спеченный |
3 |
65 |
0,1 |
1,5 |
0,04 |
- |
Плавленый |
HSMM, Китай |
5 |
58 |
0,06 |
1,5 |
0,03 |
0,04 |
Спеченный |
ГОСТ 475-89 |
1; 2 |
65 |
0,03 |
1,0 |
0,02 |
0,02 |
Плавленый |
4; 6 |
60 |
0,06 |
1,0 |
0,04 |
0,04 |
Спеченный |
ISO 5448-81 |
2,0-4,0 |
45-75 |
0,1 |
1,5 |
0,03 |
0,025 |
Плавленый |
4,0-10,0 |
Спеченный |
ASTM A101-04 |
5-6 |
63-72 |
0,01 |
2,0 |
0,03 |
0,03 |
Спеченный |
1-5 |
62-70 |
0,1 |
1,0 |
0,03 |
0,025 |
Плавленый |
*Минимальная доля азота и хрома, максимальная - остальных элементов
В Советском Союзе был разработан усовершенствованный вариант производства низкоуглеродистого феррохрома в вакуумтермических печах, который также применялся для получения спеченного высокоазотированного феррохрома. Технология была освоена на Актюбинском заводе ферросплавов. В 80-е годы объем производства азотированного феррохрома достигал здесь 1500-2000 т/год. Продукт содержал до 8 % N и использовался для выплавки широкой номенклатуры азотсодержащих хромистых сталей. Вместе с тем, вакуумтермическая технология производства отличалась большой продолжительностью и большими энергозатратами (полный цикл процесса ~9 суток, расход электроэнергии 9500 кВтч/т). Из-за высокой чувствительности процесса к перепадам температуры и давления азот неравномерно распределялся как по объему всей садки, так и по объему отдельных брикетов. Стремление достичь низкой концентрации углерода (0,03-0,06 %) приводило к завышению остаточного содержания в продукте кислорода, что было одной из причин снижения степени усвоения азота, а также роста количества неметаллических включений в стали. Нитрид хрома, используемый преимущественно для выплавки азотсодержащих суперсплавов на никелевой и кобальтовой основах, получают высокотемпературной обработкой в твердом состоянии порошков металлотермического хрома. Для этих целей используется либо электролитический металл (ERAMET COMILOG, США) либо металлотермический (DELACHAUX, Франция, LSM, Великобритания). Составы продукции различных производителей близки и соответствуют по концентрации азота более термостабильному нитриду Cr2N (Таблица 2).
Таблица 2. Примерный состав нитрида хрома*
Фирма-производитель |
N |
Cr |
C |
Si |
P |
S |
Примечание |
Eramet Comilog, США |
10,0 |
86,0 |
0,15 |
0,1 |
0,01 |
0,002 |
Гранулы 1,5х1 дюймов, 5.11 г/см3 |
Delachaux, Франция |
9,0 |
balance |
0,05 |
0,08 |
Fe 0,15 |
Al 0,1 |
Брикеты |
HCST, Германия |
12,0 |
86,0 |
0,08 |
- |
Fe 0,5 |
- |
Порошок < 0,01 и < 0,025 мм |
LSM, Великобритания |
8,5 |
balance |
0,2 |
0,25 |
0,02 |
Al 0,2 |
Брикеты, порошок < 0,3 мм |
*Минимальная доля азота и хрома, максимальная - остальных элементов
Реальной альтернативой вакуумтермической технологии производства азотированного феррохрома и хрома может стать СВС-метод, который ранее был успешно применен для производства азотированного ферросилиция. Выигрышными сторонами технологии СВС или синтеза горением являются низкие затраты энергоресурсов, максимальная скорость процесса и, наверное, самое главное то, что она позволяет получать материалы с совокупностью свойств, недостижимой для обычной технологии. Основой для реализации любого процесса в самоподдерживающемся режиме горения является сильная экзотермичность реакции взаимодействия компонентов СВС-шихты. Для системы хром-азот это условие выполняется. При образовании известных в этой системе нитридов Cr2N и CrN выделяется значительное количество тепла соответственно 25,2 и 28,2 ккал/моль. Рассчитанные по ним адиабатические температуры горения по методике составили соответственно 1290 ˚C (Cr2N) и 2060 ˚C (CrN). Хотя экзотермичность реакций образования нитридов хрома значительно меньше экзотермичности соответствующих реакций для металлов IV-V групп Периодической системы (например, для Ti и Zr Tag≈4500 ˚C, а для VN и NbN Tag≈3200 ˚C), её оказалось вполне достаточно для осуществления процесса в режиме самораспространения. Более того, подбирая оптимальные условия синтеза, горение удалось реализовать в еще менее экзотермичной системе феррохром-азот. Так как при образовании нитридов железа тепловыделение практически отсутствует, а сами нитриды (Fe4N, Fe2N) термически нестабильны, то железо играет здесь роль теплового балласта.
При осуществлении лабораторных исследований по получению азотированного феррохрома использовали порошки хрома гидридно-кальциевого марки ПХ1С по ТУ 14-1-1474-75 и алюминотермического марки ПХА97,5 по ТУ14-00186482-051-2005, а также порошок феррохрома низкоуглеродистого алюминотермического по ГОСТ 4757-91 марки ПФН различного состава, а сами исследования осуществлялись по методике, изложенной в предыдущей работе (Перспективы производства и применения СВС-нитрида ферросилиция), аналогично азотированию других металлов и ферросплавов в режиме горения. Важнейшим параметром, характеризующим такой режим горения, является давление азота в окружающем горящий порошок объеме. На рис.1 представлена зависимость скорости горения порошка феррохрома с 75,6 % Cr от давления азота; здесь же для сравнения приведены аналогичные зависимости для стандартных сплавов ферротитана (марка ФТи70, 70,6 % Ti), феррованадия (марка ФВд75У0,1, 71,6 % V) и феррониобия (марка ФНб60, 60,6 % Nb). Во всех случаях использовался порошок с размером частиц менее 0,04 мм.
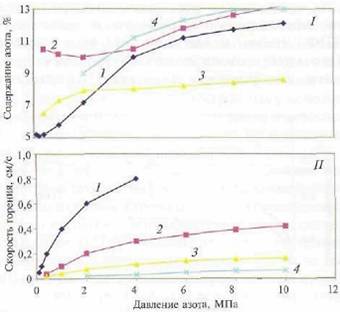
Рис. 1. Влияние давления азота на степень азотирования (I) и скорость горения (II) ферросплавов:
1 - ферротитан; 2 - феррованадий; 3 - феррониобий; 4 - феррохром
Порошки сжигались без принудительного уплотнения в цилиндрических газопроницаемых оболочках различного диаметра. Пористость исходных образцов составляла ~60 %. Во всех случаях скорость горения увеличивалась с повышением давления вследствие улучшения условий для фильтрации азота. Как и ожидалось самым медленно горящим сплавом оказался феррохром. Причиной этого является как меньшая экзотермичность реакций образования нитридов хрома по сравнению с металлами IV-V групп Периодической системы, так и то, что взаимодействие феррохрома с азотом в волне горения происходит по твердофазному механизму. Температура плавления низкоуглеродистого феррохрома лежит в интервале 1550-1670 ˚C. Даже с учетом того, что азот, растворяясь в феррохроме, несколько снижает температуру появления жидкой фазы, она оказывается все же выше температуры горения. Во всем исследованном диапазоне давлений (1,0-12,0 МПа) измеренная термопарным методом температура горения не превышала 1300 ˚C. Металлографический анализ продуктов горения подтвердил отсутствие следов плавления какой либо фазы в системе Cr-Fe-N.
Твердофазный механизм обычно способствует достижению высокой степени азотирования как металлов так и ферросплавов. Ранее возможность стадийного насыщения порошка азотом была обнаружена при получении азотированного феррованадия и азотированного ферросилиция. Большая часть азота поглощается сплавом непосредственно в волне синтеза в т.ч. режиме послойного горения. Не прореагировавшая часть ферросплава взаимодействует с азотом уже в режиме объемного догорания. Этому способствует сохранившаяся за фронтом горения высокая пористость. За счет такого дореагирования–догорания содержание азота в продукте может увеличиться на 10-40% в зависимости от условий процесса и состава исходного сплава. Однако, следует отметить, что даже при самых оптимальных условиях горения и догорания при азотировании феррохрома не удалось достичь максимального значения степени азотирования. Если для сплава с 75,6 % Cr предельная расчетная концентрация азота при условии превращения всего хрома в нитрид CrN1,0 составляет ~16,8 % N, то реально достигнутое максимальное содержание азота в феррохроме составило ~13,0 % N. Таким образом, степень азотирования достигла чуть более 77 % от расчетной.
Близкая к 100 % максимальная степень азотирования была получена при получении азотированного хрома. На рис. 2 представлены зависимости скорости и температуры горения, а также степени азотирования гидридно-кальциевого порошка хрома с размером частиц менее 0,02 мм. В интервале давлений 0,1-0,9 МПа все три параметра монотонно увеличиваются. При максимальном давлении практически весь хром превращается в мононитрид CrN. Рентгенографически продукт, синтезированный при давлении свыше 3,0 МПа, является однофазным. При минимальном давлении (0,1-0,2 МПа) основу сгоревшего материала составляет полунитрид хрома Cr2N при этом обнаруживаются линии, относящиеся к нитриду CrN и свободному хрому. С повышением давления доля мононитрида быстро увеличивается.
Рис. 2. Влияние давления азота на скорость горения (1, 4), степень азотирования (3, 5) и температуру горения (2); 1, 2, 3 - хром; 4, 5, 6 - феррохром
Порошок хрома алюминотермического оказался менее активным по сравнению с порошком гидридно-кальциевого передела. Основная причина такой высокой реакционной способности кроется в большей удельной поверхности порошка, обусловленной высокой его дисперсностью. Микроскопический анализ показал, что в гидридно-кальциевом хроме даже сравнительно крупные частицы (~0,04-0,05 мм) фактически представляют собой спекшиеся конгломераты более мелких порошинок, размер которых не превышает ~0,01 мм. В то же время в порошке металлотермического хрома, отсеянного через сито 0,04 мм, превалирует доля частиц более 0,01 мм. Аналогичная картина наблюдается и для порошка феррохрома. Вследствие высокой прочности низкоуглеродистого феррохрома и металлического хрома алюминотермического восстановления, получение тонких порошков требует больших энергозатрат. Из рис. 2 видно, что скорость горения и степень азотирования порошка хрома металлотермического значительно ниже соответствующих параметров для гидридно-кальциевого порошка. Так как глубина превращения хрома алюминотермического лежит в пределах 70,7 % (15,0 % N) – 82,1 % (17,4 % N), то продукт горения остается двухфазным, включающим оба нитрида хрома.
В отличие от хрома продукты горения феррохрома всегда многофазны. Рентгенографически обнаруживаются альфа-железо, двойной нитрид (Fe,Cr)2N и мононитрид CrN. Причем во всем интервале давлений качественно такой фазовый состав сохраняется. При увеличении степени азотирования, достигаемой повышением давления, растет доля мононитрида хрома и свободного железа. Такая же тенденция в изменении фазового состава продуктов азотирования феррохрома была обнаружена ранее при печном синтезе.
На основе результатов, полученных при проведении лабораторных исследований и испытаний, в «НТПФ «Эталон» была разработана и освоена промышленная СВС-технология производства азотированных легирующих материалов на основе хрома. Для использования в сталеплавильном производстве предлагаются 4 марки принципиально новых высокоазотистых лигатур: спеченный и плавленый азотированный хром, спеченный и плавленый азотированный феррохром. В таблице 3 представлены химический и фазовый состав новых сплавов, а также их плотность. А на рис. 3 можно видеть макро- и микроструктуру новых сплавов.
Таблица 3. Химический состав и свойства СВС-сплавов*
Показатель |
Нитрид феррохрома |
Нитрид хрома |
Химический состав, %: |
N |
6-8 |
8-13 |
8-12 |
16-20 |
Cr |
62-76 |
60-72 |
88-91 |
79-82 |
C |
0,05 |
0,05 |
0,03 |
0,03 |
Al |
0,10 |
0,10 |
0,06 |
0,06 |
O |
0,3 |
0,3 |
0,2 |
0,2 |
Фазовый состав |
(Fe, Cr)2N, Fe |
(Fe, Cr)2N, CrN, Fe |
Cr2N |
CrN, Cr2N |
Плотность, г/см3
| 6,0-7,0 |
4,3-5,3 |
5,5-6,6 |
3,4-4,6 |
*Минимальная доля для азота и хрома, максимальная - остальных элементов
Рис. 3. Макроструктура новых азотированных сплавов:
1, 2 - хром плавленный и спеченный; 3, 4 - феррохром плавленый и спеченный
Азотированный феррохром предназначен для выплавки азотсодержащих нержавеющих сталей, а также других марок хромсодержащих сталей с азотом. Азотированный хром рекомендуется для преимущественного использования при выплавке высокоазотистых суперсплавов на хромоникелевой основе, а также для высоколегированных нержавеющих сталей с максимальной концентрацией азота. Плавленые феррохром и хром эффективно применять в традиционном кусковом виде для легирования непосредственно в печи либо в ковше при переливе в него расплава. Спеченные лигатуры наряду с традиционным способом введения целесообразно использовать в виде порошковой проволоки. Вследствие высокой концентрации азота расход такой проволоки будет минимальным при высоком и стабильном усвоении азота расплавом.
Новые азотсодержащие лигатуры на основе хрома прошли успешные испытания на ряде предприятий России и за рубежом при производстве различных марок сталей. Марочное содержание азота в полученном металле изменялось в широких пределах от 0,04 до 0,6 % N. В частности, были выплавлены такие сорта стали как 12Х18АГ18, 35Х2АФ, 55Х21Г9АН4, 110Г13ХФАЛ и пр., а также хромоникелевый сплав с ~0,5 % N. Металл выплавлялся в электропечах с использованием различных марок азотированного феррохрома и хрома, содержащих от 9,0 до 19,5 % N. Во всех случаях степень усвоения азота превышала 90 %.
Таким образом, в России впервые создана промышленная технология производства азотсодержащих легирующих сплавов хрома на основе метода самораспространяющегося высокотемпературного синтеза. Созданные в «НТПФ «Эталон» на базе новой технологии легирующие материалы на основе хрома не имеют аналогов. Азотированный хром и азотированный феррохром, сочетая высокую концентрацию азота с максимальной плотностью, позволяют экономически эффективно выплавлять азотсодержащие стали самой широкой номенклатуры.
Производимый ООО "НТПФ "Эталон"
Другие материалы по теме