Страница для печатиЗиатдинов Мансур Хузиахметович, канд. техн. наук,
Шатохин Игорь Михайлович, д-р техн. наук
ООО "НТПФ "Эталон"
Важнейшей тенденцией совершенствования одной из самых ресурсозатратных современных отраслей промышленности - металлургии - является стремление к уменьшению расхода ресурсов, как материальных и энергетических, так людских, экологических и др. В сталеплавильном производстве, наряду с другими направлениями экономии, это проявляется, в частности, в увеличении объемов и расширении сортамента выплавки микролегированной стали, а так же в уменьшении удельных затрат огнеупорных материалов, так как эти легирующие материалы и огнеупоры являются неотъемлемыми в металлургии и занимают значительную долю в себестоимости стальной продукции. Для микролегирования используют как традиционные элементы, так и сравнительно новые, такие как азот и бор. Несомненным преимуществом последних является неограниченность запасов в природе и экологическая безопасность, а положительное влияние их на свойства готовой стали проявляется при очень низких концентрациях. В настоящее время высокоазотистые коррозионностойкие стали эффективно используются в энергетическом машино- и двигателестроении, химической и других отраслях промышленности, а высокобористые коррозионностойкие стали незаменимы в атомной энергетике. Однако наибольшее распространение получили стали с микродобавками азота и бора. Широко известны высокопрочные низколегированные стали с нитридным и карбонитридным упрочнением для самого широкого спектра применения. Стали с микродобавками бора применяют везде, где требуется сочетание высокой прочности, вязкости и износостойкости. В последние годы появились новые области применения сталей, микролегированных бором и азотом. Например, при производстве анизотропной электротехнической стали за счет введения небольших количеств азота были достигнуты высокие значения эксплуатационных характеристик металла, а микродобавки бора в сочетании с другими микролегирующими элементами позволили создать новую трубную сталь категории прочности X120.
Что касается огнеупоров, то их производители не только стараются повышать качество традиционно применяемых материалов, но все большее внимание уделяют использованию новых материалов для улучшения качества продукции. В частности, увеличивается объем потребления и расширяется номенклатура огнеупоров, содержащих тугоплавкие неорганические соединения, такие как нитриды, бориды, карбиды и другие. Например, эти соединения показали высокую эффективность в качестве антиоксидантов в углеродистых огнеупорах, в качестве упрочняющих добавок в неформованных огнеупорах, а также в спеченных огнеупорных изделиях. Бескислородные тугоплавкие неорганические соединения, обладая уникальными физико-химическими и механическими свойствами, позволяют качественно улучшить эксплуатационные характеристики многих огнеупорных материалов. В отличие от природных оксидных огнеупоров, все без исключения бескислородные огнеупорные материалы являются синтезируемыми. Для их производства были разработаны самые разные способы получения, но в промышленных масштабах наибольшее распространен печной синтез. Высокотемпературной обработкой металлов и неметаллов и/или их оксидов в вакууме либо инертной атмосфере получают требуемые соединения:
TiO2 + 3C → TiC + 2CO,
TiO2 + B2O3 + 5C → TiB2 + 5CO,
2Ti + N2 → TiN.
Довольно часто оказывается гораздо эффективнее применение сравнительно нового способа получения таких соединений, а именно метода самораспространяющегося высокотемпературного синтеза (СВС). СВС или синтез горением - это отечественный технологический процесс, предложенный учеными АН СССР под руководством акад. А.Г.Мержанова более 40 лет назад. В традиционном смысле под горением понимается протекание экзотермических химических реакций окисления, в результате которых выделяется тепло и образуются твердые либо газообразные продукты горения. Например, применительно к углю основными продуктами его горения будут углекислый газ и зола. Следовательно, в повседневной жизни мы чаще всего сталкиваемся с так называемым энергетическим горением, когда единственной целью осуществления процесса является получение тепловой энергии. Иногда также используется образующаяся как побочный продукт зола: древесная в качестве удобрения, угольная - как строительный материал, а зола от сжигания некоторых сортов нефти является источником минерального сырья, в частности, пентаоксид ванадия и т.д.
Однако известны производственные процессы, в которых горение осуществляется не для получения тепла, а для производства, условно говоря, золы. Такое горение часто называют технологическим. К нему можно отнести следующие производства: получение сажи путем неполного сгорания природного газа, получение оксидов цветных металлов путем обжига сульфидов, получение металлов и сплавов металлотермическим восстановлением оксидов и некоторые другие. При металлотермическом процессе, наиболее близком сталеплавильщикам, экзотермическая реакция горения используется для производства различных ферросплавов и лигатур:
Cr2O3 + Al(Fe) → Al2O3 + Cr(Fe,Al) + Q;
V2O5 + Al(Fe) → Al2O3 + V(Fe,Al) + Q.
Как видим, в результате такого окислительно-восстановительного горения образуются три продукта: целевой металлический сплав, оксидный шлак и тепловая энергия. Последние два для данного процесса являются отходами, которые иногда могут утилизироваться. Переходя к детальному рассмотрению СВС-процесса, еще раз отметим, что в основе как энергетического, так и в приведенных примерах традиционного технологического горения лежит окислительный процесс, в котором обязательно участвует кислород.
Отличительной особенностью классического СВС-метода является проведения самоподдерживающегося процесса горения за счет выделевшегося в результате реакций прямого синтеза тепла:
Ti + C → TiC + Q;
2V + N2 → 2VN + Q;
Ni + Al → NiAl + Q и т.д.
В СВС-реакциях кислород отсутствует. Здесь роль окислителя выполняют различные неметаллы - С, В, N, Н и др., а при синтезе интерметаллидов - даже металлы. Другим принципиальным отличием СВС-процесса является отсутствие каких-либо отходов, твердых либо газообразных. Среди технологически выгодных сторон этого метода отметим его скоротечность, а значит, и высокую производительность, отсутствие затрат электроэнергии, простоту конструкции СВС-реакторов.
Однако, несмотря на это, примеров по-настоящему промышленного применения СВС-технологии до настоящего времени практически нет. Причин для этого несколько. Во-первых, неготовность самой промышленности к использованию во многом уникальной СВС-продукции. Во-вторых, отсутствие отработанной промышленной технологии и оборудования. В-третьих, при создании опытных производств выявилась повышенная опасность СВС-процесса, связанная с необходимостью использования в качестве сырья высокоактивных тонких порошков, а также с сочетанием высокого давления и экстремальных температур. И, наконец, сама суть СВС-технологии, как процесса самораспространяющегося, а значит трудноуправляемого, также не внушает оптимизма производственникам. В действительности же в большинстве случаев причина кроется в высокой стоимости СВС-процесса, которая обусловлена необходимостью применения в качестве сырья дорогих тонкодисперсных порошков чистых металлов и неметаллов. Таким образом происходит аннулирование полученных выгод в результате энергонезатратного СВС-процесса за счет дорогих исходных реагентов, при производстве которых с лихвой используется электроэнергия. Поэтому, несмотря на явное наличие потенциальных областей применения СВС-технологии и СВС-материалов в металлургии, отсутствие экономически оправданных вариантов решения проблемы сырья тормозит освоение в металлургических производствах в общем-то передового процесса. К тому же сами масштабы потребностей этих производств были не сопоставимы практически с пробирочным уровнем получения СВС-материалов.
Проблема была решена за счет перехода на металлургическое сырье, более дешевое, более доступное и более известное металлургам. А именно - был предложен вариант СВС-процесса, основанный на обменных экзотермических реакциях:
FeTi + C → TiC + Fe,
FeV + ½N2 → VN + Fe,
3FeSi2 + 4N2 → 2Si3N4 + 3Fe,
2FeB + Ti → TiB2 + 2Fe,
FeS + Mn → MnS + Fe,
Fe2N + Ti → TiN + Fe.
Как видим, в новой схеме реализации СВС-реакций основными сырьевыми материалами являются ферросплавы, представляющие собой различные соединения железа с легирующими и раскисляющими элементами стали. Основу таких ферросплавов составляют интерметаллиды (FeV, FeTi, Fe2Nb), бориды (FeB, FeBn), силициды (FeSi, FeSi2, MnSi2,), твердые растворы (Fe-Cr, Fe-Mn) и др., а также смеси этих фаз. Позже для производства СВС-продукции для металлургии начали использовать и другие материалы металлургического передела, такие как сульфиды (FeS), карбиды (SiC, В4С), и др. Внешне новый металлургический тип СВС-реакций более близок к металлотермии, чем к классическому синтезу горением:
Ti + B → TiB2,
Ti + FeB → TiB2 + Fe,
2Al + Cr2O3 → Al2O3 + 2Cr.
Однако он принципиально отличается от окислительно-восстановительной реакции отсутствием шлаков-отходов. Весь образующийся материал - композиция борид ферротитана (Fe-TiB2,) - является целевым материалом. При металлургическом СВС-процессе нет фазоразделения, а продукт является композиционным материалом на основе тугоплавкого неорганического соединения (в приведенном примере TiB2,), связкой для которого служит железо или, чаще всего, различные сплавы на его основе. Само горение, как и в классическом СВС-процессе, происходит без участия кислорода.
Известно, что для стабильного проведения металлотермических реакций необходимым условием является достижение температур горения, значительно превышающих температуры плавления всех компонентов продукта горения. Требуется это для того, чтобы произошло полное разделение металлической и шлаковой составляющих продуктов реакции. В то же время при осуществлении СВС-обменных реакций температура горения выбирается таким образом, чтобы она не превышала температуры плавления хотя бы одного из компонентов продуктов горения, обычного тугоплавкого неорганического соединения. Такой выбор необходим для того, чтобы в результате синтеза образовался продукт с типичной композиционной структурой, исключались бы ликвация и фазоразделение и достигалось равномерное распределение фаз по объему (рисунок 1).
Рисунок 1. Типичная микроструктура композиции TiB2-Fe:
1 - TiB2; 2 - Fe
Исторически впервые металлургический СВС-процесс был осуществлен для получения азотированного феррованадия, который предназначался для выплавки низколегированных сталей с нитридным упрочнением. Сырьем для синтеза горением служил стандартный силикотермическнй феррованадий с содержанием ванадия 40-50 %, представляющий собой интерметаллид эквиатонного состава со структурой σ-фазы. Реакция азотирования происходит в результате вытеснения железа азотом с образованием мононитрида ванадия (VN) и выделением свободного α-железа. Высвободившегося при нитридообразовании тепла достаточно для полного расплавления железа и образования слитка. При этом температура горения (1450-1550 °С) много ниже температуры плавления нитрида ванадия (2050 °С). В окончательном виде азотированный феррованадий представляет собой литой композиционный материал, основу которого составляет δ-нитрид ванадия (55-68 % по объему), связкой для которого служит железо. Плотность такого материала близка к плотности жидкой стали (≈6,5 г/см3), а количество азота изменяется в пределах 9-11 %. Благодаря высокой плотности достигается практически полное усвоение азота из плавленого азотированного феррованадия, а в сочетании с высокой концентрацией в нем азота обеспечивается минимальный расход лигатуры.
Как и в металлотермии, для успешного проведения СВС-процесса необходима высокая экзотермичность реакций. При образовании многих практически важных тугоплавких неорганических соединений тепловой эффект их образования значителен. В качестве иллюстрации в таблице 1 представлены значения тепловых эффектов образования некоторых соединений и рассчитанные по ним адиабатические температуры горения (максимальные температуры разогрева, которые могут быть достигнуты при реализации реакций без учета теплопотерь). Видно, что такой разогрев в СВС-реакциях вполне сопоставим с разогревом, достигаемым в восстановительных металлотермических реакциях. Ситуация усложняется в случае использования в СВС-реакциях в качестве реагентов ферросплавов и других соединений. В этом случае экзотермический эффект сильно снижается, чему способствуют как наличие энергетически нейтрального железа, так и расходование части тепла на разложение в исходных ферросплавах различных термостойких соединений (силицидов, карбидов, интерметаллидов и др.). В связи с тем, что при образовании нитридов железа (Fe2N, Fe4N) практически отсутствует тепловыделение, с ростом концентрации железа адиабатическая температура горения сплавов будет быстро снижаться. Однако при этом для практически важных сплавов (с 40-80 % легирующего элемента) она остается достаточно высокой.
Таблица 1. Тепловой эффект образования некоторых тугоплавких соединений
Реакция |
Тепловой эффект реакции, кал/г |
Адиабатическая температура горения, °С |
Температура плавления продукта, °С |
Классический СВС |
V + ½N2 → VN |
924 |
3300 |
2050 |
Zr + 2B → ZrB2 |
647 |
3040 |
3040 |
Ti + 2C → TiC2 |
736 |
2940 |
2940 |
Mo + 2Si2 → MoSi2 |
207 |
1630 |
2030 |
Металлотермия |
2Al + Cr2O3 → Al2O3 + 2Cr |
726 |
1800 |
2050 |
2Fe2O3 + 3Si → 3SiO2 + 4Fe |
589 |
2300 |
1730 |
MoO3 + 7/2Si → MoSi2 + 3/2SiO2 |
685 |
2300 |
2020 |
Рассмотрим на двух примерах более подробно получение с помощью СВС-обменных реакций композиционных материалов для сталеплавильного производства - синтез азотированного ферросилиция и борида ферротитана. Выбор этих реакций обусловлен тем, что они относятся к различным типам СВС-процесса: фильтрационному и безгазовому. Из определения понятно, что в первом случае одним из реагентов реакции является газ, а во втором - все компоненты смеси - конденсированные вещества. При фильтрационном режиме горения газообразный реагент (азот) поступает в зону взаимодействия путем фильтрации из окружающего объема. Наиболее ярким внешним проявлением такого горения является сильная зависимость скорости горения от давления газа. В случае безгазового горения влияние давления газа на скорость горения отсутствует, ибо все участвующие в химическом взаимодействии реагенты и продукты синтеза (включая промежуточные) в зоне горения находятся в твердом либо жидком состоянии. На рисунке 2, а представлена зависимость скорости горения от давления для выбранных систем. При горении смеси (Fe-B)-Ti варьировали давление аргона, а при азотировании (Fe—Si) - азота.
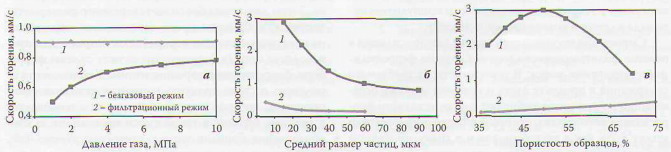
Рисунок 2. Зависимость скорости горения от давления газа (а),
дисперсности порошка ферросплава (б) и пористости шихты (в):
1 - (Fe-B)-Ti, 2 - (Fe-Si)-N2
Общим как для фильтрационного, так и для безгазового горения является сильная зависимость скорости и режимов горения и самой возможности осуществления процесса от размеров частиц реагентов. Для того, чтобы осуществить процесс в самоподдерживающемся режиме, необходимо обеспечить высокий уровень скорости тепловыделения. Для достижения этого исходные компоненты шихты должны иметь максимальную поверхность взаимодействия, что, в конечном счете, определяется размером их частиц. Из графиков зависимости скорости распространения волны горения от дисперсности сырьевых материалов (рисунок 2, б) видно, что в обоих случаях с ростом размеров частиц скорость горения быстро снижается, и далее при еще достаточно высокой дисперсности горение в самоподдерживающемся режиме становится невозможным.
Так как распространение волны горения происходит в пористой порошковой среде, то и в безгазовом и в фильтрационном режимах горения величина пористости материала оказывает сильное влияние на характер распространения волны горения. Однако механизм такого влияния для каждого режима свой. Общим является то, что по мере уменьшения пористости растет теплопроводность шихты за счет улучшения контакта между частицами. Поначалу это приводит к росту скорости горения (рисунок 2, в, кривая 1), но в дальнейшем скорость горения начинает постепенно уменьшаться, и горение становится невозможным.
Связано это с тем, что дальнейший рост теплопроводности приводит к ускорению диссипации энергии из зоны горения: скорость теплоотвода из зоны реакции начинает превалировать над скоростью тепловыделения, и процесс останавливается.
В случае фильтрационного горения на механизм теплофизического воздействия пористости накладывается влияние фильтрационного механизма. Поэтому скорость горения ферросилиция постоянно снижается при уменьшении пористости во всем диапазоне ее изменения, ибо быстро нарастают затруднения для доставки азота извне. Причиной этого является недостаток азота в порах шихты для поддержания горения даже при относительно высоком давлении (до 12 МПа).
Дальнейшие исследования выбранных систем показали, что кроме давления азота, дисперсности порошков шихтовых материалов и пористости самой шихты на развитие процесса СВС сильно влияют такие исходные параметры, как соотношение компонентов в смеси, содержание активного компонента в ферросплаве, состав и количество примесей, состав окружающей газовой среды, размер установки для синтеза и т.д. Анализ влияния всех этих параметров позволил разработать режимы реализации процесса в промышленных условиях. При получении азотированного ферросилиция оптимальные условия процесса стабильного горения создаются при следующих параметрах:
Содержание кремния в исходном ферросилиции, % |
45-80 |
Содержание примесей в исходном ферросилиции, % |
Не более 3 |
Дисперсность порошка исходного ферросилиция, мкм |
δ50 ≈5 |
Пористость шихты, % |
40-60 |
Единовременная загрузка исходной шихты, т |
0,10-0,15 |
Давление азота, МПа |
6,0-15,0 |
Температура горения, °С |
1800-2200 |
При производстве борида ферротитана важным дополнительным условием его получения является создание внутри СВС-реактора атмосферы, исключающей окисление продукта во время горения. В зависимости от требований к чистоте продукции по кислороду, синтез осуществляется либо в вакууме, либо в атмосфере аргона высокой чистоты или другого инертного газа. Специально для этих целей в НТПФ «ЭТАЛОН» был разработан промышленный СВС-реактор с рабочим объемом 0,15 м3, способный работать как в вакууме, так и в атмосфере газа при высоком давлении (до 15 МПа) (рисунок 3). Корпус установки изготовлен из толстостенной металлической трубы. Специальное запирающее устройство обеспечивает герметичность во время горения, а также быстрое открытие-закрытие установки при загрузке сырья и выгрузке продукта. С внутренней стороны реактора имеется зажигающее устройство для локального нагрева исходной шихты, инициирования процессов воспламенения и последующего горения в послойном и объемном режимах.
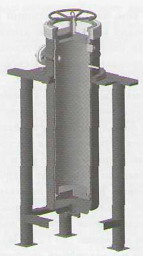
Рисунок 3. Схема промышленного СВС-реактора
Как уже отмечалось, СВС-реакции сильно экзотермичны. Например, при превращении 1 кг кремния в нитрид выделяется около 8925 кДж тепла. Во время горения скорость тепловыделения составляет порядка 419-628,5 кДж/с. Для нейтрализации столь интенсивного выделения энергии СВС-реактор снабжен системой охлаждения. Как и во многих металлургических агрегатах, охлаждение осуществляется водой, циркулирующей по водяной рубашке. Регулируя скорость подачи воды, можно на выходе из реактора получать нагретую до различной температуры воду. При необходимости температура воды может быть повышена на 10-50 °С. Режим нагрева до максимальной температуры реализуется в холодное время года, нагретая вода используется в системе отопления производственных помещений. В теплый период времени подогретая вода поступает в устройство интенсивного принудительного охлаждения и возвращается в систему.
Сырьем для производства азотированного ферросилиция в режиме фильтрационного горения служит ферросилиций обычных гостовых марок. В зависимости от необходимого содержания в азота и кремния в готовом продукте, а также ограничений по примесям, выбирают конкретный состав исходного ферросилиция, который при поставке может быть как в кусковом, так и в гранулированном или порошковом виде. Из полученного сырья с помощью установок дробления, измельчения и классификации получают исходный порошок ферросилиция требуемой фракции (650 ~ 5 мкм). Комплекс дробильно-помольного отделения для шихтоподготовки включает дробилки щековые различных типов и размеров, в том числе собственного производства, конусные инерционные дробилки, вибромельницы и импульсные пневмоизмельчители.
Порошок ферросилиция, доведенный до необходимой дисперсности, при помощи специальных пневматических устройств загружается в металлические корзины. Корзины устанавливаются в СВС-реактор. После этого реактор герметизируется и заполняется азотом до необходимого рабочего давления. Кратковременной подачей электроимпульса на запальное устройство инициируется очаг экзотермической реакции образования нитрида кремния, температура в которой достигает температуры горения (≈2000 °С). Далее реакция азотирования возбуждается в следующем слое шихты и таким образом, послойно, происходит насыщение ферросилиция азотом. Скорость распространения такой волны экзотермической реакции (скорость горения) в зависимости от состава исходной шихты может изменяться в пределах 0,1-0,8 мм/с. Высокая температура, развивающаяся в волне горения, способствует спеканию продукта в брикеты высокой прочности. Прочность брикетов при сжатии в зависимости от условий азотирования и состава исходной шихты составляет 20-100 МПа.
После окончания процесса азотирования продукт остывает в реакторе в атмосфере азота. Затем давление сбрасывается, реактор разгерметизируется, и брикеты извлекаются и после взвешивания передаются на следующую стадию переработки. Сырьем для производства борида ферротитана служат сплавы ферробора, ферротитана и порошок титана. В зависимости от целевого состава продукта готовится исходная смесь порошков, которая загружается в тигли и помещается в реактор. Горение в такой смеси происходит за счет образования боридов титана, преимущественно TiB2. Эта реакция сильно экзотермична, расчетная температура Тad = 2900 °С. При синтезе композиции TiB2-Fe из сплавов фактическая температура горения много ниже. Так, при использовании исходного ферробора с содержанием 20% В, измеренная температура горения составила около 1450 °С. В отличие от нитрида ферросилиция, борид ферротитана синтезируется в инертной атмосфере. При необходимости производства особо чистых материалов, например, для легирования трубной стали, синтез осуществляется в вакууме.
Наряду с нитридом ферросилиция, выпускаемым под торговой маркой NITRO-FESIL® и боридом ферротитана, НТПФ «ЭТАЛОН» разработал целую серию новых сталей и сплавов с азотом и бором (таблица 2), Особенностью СВС-технологии получения легирующих материалов является то, что она позволяет производить продукцию с самым широким комплексом свойств, которых зачастую невозможно достичь при использовании обычной печной технологии. Например, только СВС-технология обеспечивает производство азотированных лигатур, сочетающих высокую плотность с максимальным содержанием азота, в частности, таких как плавленый азотированный феррованадий, плавленый азотированный феррохром (хром) и другие.
Таблица 2. Новые композиционные легирующие сплавы, разработанные НТПФ "Эталон"
Наименование продукции |
Содержание основного элемента |
Область применения |
Нитрид ферросилиция Si3N4-Fe(Si) |
50-80 |
Сталь электротехническая, неформованные огнеупоры |
Азотированный феррохром CrN-Cr2N-Fe |
75-80 |
Сталь нержавеющая |
Нитрид хрома CrN-Cr2N |
95-99 |
Суперсплавы |
Азотированный феррованадий VN-Fe |
55-68 |
Сталь низколегированная, рельсовая |
Нитрид силикомарганца Mn4N-Si3N4 |
90-95 |
Сталь марганцовистая |
Борид ферротитана TiB2-Fe(Ti) |
50-65 |
Сталь борсодержащая трубная |
Борид феррониобия NbB2-Fe |
70-80 |
IF-сталь |
Сульфид ферромарганца MnS-Fe |
50-60 |
Сталь автоматная |
Композиции, образующиеся при осуществлении СВ-синтеза, могут быть использованы в качестве компонентов различных огнеупорных материалов. В частности, в НТПФ «Эталон» разработана серия упрочняющих добавок на основе нитрида кремния с ферросилицидной связкой для производства высокоэффективных леточных и желобиых масс. Разработана и испытана композиция SiC-Si3N4, для получения огнеупорных изделий для доменного производства и производства алюминия. Получены положительные результаты по использованию композиций на основе боридов титана в качестве антиоксидантов в периклазуглеродистых огнеупорах. Отработана технология производства порошков боридных антиоксидантов субмикронного размера. Продолжаются исследования и испытания наиболее перспективных комплексных антиоксидантов борид-карбидного и борид-нитридного классов. Начаты исследования по изучению возможности применения СВС-материалов, разработанных в НТПФ «Эталон» для использования в составе защитных покрытий конвертерных и доменных фурм и другого оборудования, эксплуатирующегося в экстремальных условиях.
Композиционные материалы на основе тугоплавких неорганических соединений успешно испытаны в промышленных условиях на металлургических предприятиях России. Пионером в освоении новых композиций, безусловно, является ОАО ММК. Здесь впервые была освоена комплексная технология выплавки стали, микролегированной азотом, с использованием СВС-азотированного ферросилиция марки NITRO-FESIL®. Последовательно вводя композицию в кусковом виде и в виде порошковой проволоки, удалось получить стабильные концентрации азота в узких пределах, доведя выход металла по азоту практически до 100 %. Аналогичная технология выплавки электротехнической анизотропной стали успешно опробована в ОАО НЛМК.
Таким образом, впервые создано промышленное производство материалов на основе тугоплавких неорганических соединений, предназначенных для использования в металлургии. Технология базируется на фундаментальных принципах СВС-метода и новых технологических решениях, специально разработанных для крупнотоннажного металлургического производства.
Опубликовано в журнале "Наука. Техника. Производство". 14.10.2008 (Статья в pdf)
Ознакомиться с материалами, производимыми НТПФ "Эталон" по СВС-технологии: