Страница для печатиПредыдущая часть статьи - Производство азотированного феррованадия. Часть 3
Известно, что экономическая эффективность использования ванадия может возрасти в случае применения различных его комплексных сплавов, в том числе азотсодержащих (азотированного феррованадия). В настоящей работе исследуется возможность получения сложных азотированных ванадийсодержащих сплавов в комбинации с марганцем, ниобием и кремнием. Источниками этих компонентов служили порошки стандартных промышленных сплавов: феррониобия, марганца и ферросилиция. Несмотря на то, что теплоты образования нитридов кремния (Si3N4), ниобия (Nb6N) и марганца (Mn3N2) вполне сопоставимы с экзотермичностью нитридов ванадия, интенсивность их взаимодействия с азотом оказалась много меньше. Как видно на рис. 8, все три добавки снижают скорость горения феррованадия. Марганец и ниобий несколько уменьшают концентрацию азота в продуктах горения, а ферросилиций напротив значительно ее повышает. Таким образом, СВС-технология позволяет производить любые комплексные лигатуры, включающие V, Nb, Mn и/или Si с использованием в качестве сырья порошков стандартных ферросплавов на их основе. Концентрация азота близка к максимальным значениям, соответствующим выбранным составам.
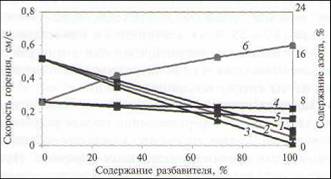
Рис. 8. Влияние разбавления ферросплавами на скорость горения (1-3) и степень азотирования феррованадия (4-6): 1 и 4 - FeNb; 2 и 5 - Mn; 3 и 6 - FeSi
Результаты лабораторных исследований, полученные с использованием промышленных феррованадиевых сплавов были использованным при создании технологии производства азотированного феррованадия на больших установках с рабочим объемом 0,15 м3. Скорость горения в таких промышленных СВС-реакторах определяется по показаниям расходомера, установленного на входе в установку. После инициирования процесса горения путем подачи электроимпульса на зажигающее устройство реактора расход азота резко возрастает, быстро достигая постоянного значения. Процесс получения азотированного феррованадия с постоянным расходом соответствует стадии послойного стационарного горения. Окончание этой стадии фиксируется расходомером также по резкому изменению скорости поглощения азота. Причем при азотировании σ-феррованадия расход азота снижается практически до нуля, что является дополнительным свидетельством об отсутствии стадии дореагирования в объемном режиме. В случае азотирования α-феррованадия после момента быстрого снижения скорости поглощения азота, фиксируемого расходомером, насыщение азота сплавом продолжается при более низком и постоянно уменьшающемся его потреблении. Измеренные таким образом скорости горения феррованадия в промышленной установке оказались близкими к результатам, полученным при азотировании на лабораторной установке. Так, например, продолжительность горения сплава марки FeV50 при давлении в 12 МПа составила ≈ 5-8 мин, что соответствует скорости послойного горения ≈ 0,2-03 см/сек. Интенсивность поглощения азота феррованадием составила ≈ 0,1 м3/с. Концентрация азота в готовом азотированном феррованадии зависит от марки исходного сплава, давления азота в СВС-реакторе во время горения, дисперсности порошка и ряда других факторов и может изменяться в пределах от 8 до 16 %.
Для достижения в продуктах горения максимального возможных (предельных) концентраций азота в работе был использован традиционный в этих случаях прием. Для снижения экзотермичности шихты в нее обычно добавляют продукты реакции, которые, во-первых, снижают температуру процесса, а с другой стороны препятствуют коагуляции частиц во фронте горения и снижению проницаемости после его прохождения, создавая тем самым условия для максимального превращения металла в нитрид при доазотировании. Влияние разбавления исходной шихты продуктами реакции было исследовано на примере горения высокопроцентного феррованадия марки FeV80 и FeV60. На рис. 9 представлена зависимость содержания азота в готовом азотированном феррованадии от количества в исходной смеси продуктов азотирования. В качестве разбавителя использовались порошки азотированного феррованадия, полученные из тех же самых ферросплавов. Дисперсия всех порошков была одинаковой: 0,04 мм порошок нитрида феррованадия, синтезированного из сплава FeV80 содержал 12,1 % N, а из смеси FeV60 – 10,9 % N. Из рисунка видим, что предельная концентрация азота в FeV80 достигается при добавлении в шихту 30 % продукта, а в FeV60 – 15 %. Скорость горения смесей при их разбавлении конечным продуктом быстро снижается при возрастании его концентрации.
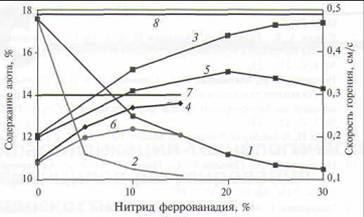
Рис. 8. Влияние разбавления продуктом на скорость горения (1 и 2) и степень азотирования (3-6) феррованадия: 1, 3, 5 - FeV80 (FeVN80; 2, 4, 6 - FeV60 (FeVN60); 3 и 4 - общее содержание азота при горении; 7 и 8 - предельное содержание азота для FeV60 (7) и FeV80 (8)
Для промышленного использования были разработаны два типа азотированного феррованадия: плавленый и спеченный. Первый предназначен для традиционного кускового легирования сталей в ковше либо непосредственно в печном агрегате. Второй сплав эффективен при использовании в качестве наполнителя порошковой проволоки и предназначен для доводки концентрации азота пред разливкой. Сырьем для синтеза плавленого нитрида феррованадия служат сплавы марок FeV40 и FeV50 по ГОСТ 2730, а для спеченного – сплавы марок FeV80. В табл. 2 приведены основные характеристики плавленого азотированного феррованадия. Здесь же для сравнения представлены те же данные для сплава типа NITROVAN и печного азотированного феррованадия по ТУ 14-5-122-80.
Таблица 2. Состав и свойства азотсодержащих сплавов ванадия
Плавленый нитрид феррованадия был использован при выплавке различных марок высокопрочных низколегированных сталей, а также рельсовой и быстрорежущей стали. Степень усвоения азота составила 86-98 %. Следует обратить внимание на то, что степень усвоения самого ванадия оказалась также исключительно высокой и достигла 95 % и более.
Таким образом, новая технология производства азотированного феррованадия, основанная на принципах металлургического СВС–процесса, позволяет получать продукцию с уникальным сочетанием высокой плотности, характерной для плавленых лигатур, с максимальным содержанием азота, характерным для спеченных легирующих материалов. Кроме того, благодаря концентрационной структуре нового сплава (αFe – δVN) плавленый азотированный феррованадий имеет высокую прочность. Вследствие этого полностью исключается разрушение сплава при различных технологических операциях, а также исключается образование не только порошкообразных (пылевидных) частиц, но и любых кусков менее 10 мм.
Начало статьи - Производство азотированного феррованадия. Часть 1
Опубликовано в журнале "Сталь". № 11. 2009 г.
Производимый ООО "НТПФ "Эталон"
Другие материалы по теме